Bridging
the Gap
How Plants Can Help Workers Cope with Change
Some plants struggle to incorporate new technology, while others adopt the unfamiliar almost without a hitch. Why the disparity? Well, the answer to that question became apparent to eChem Expo speaker Ronald Lee only after decades of running plants. “It’s because we didn’t do the right change management,” Lee said of the plants where projects faltered. “We put a lot of time into the physical and technical aspects, but we didn’t do the job on the people side.”
Lee shared advice on how to act upon that wisdom during a panel discussion called Preparing Employees to Manage the Digital Divide. He addressed the subject just 30 days after becoming Voovio Technologies vice president of operations. Before that he worked 36 years for DuPont, managing plants on several occasions as he rose to the position of global operations manager.
For change to succeed, leaders should help employees understand the importance of adopting what might seem overly novel, Lee told his eChem Expo audience. That requires explaining how change will directly alter workers’ lives and letting them know when they will feel the difference. But too often that doesn’t happen, he lamented. “We never stand face-to-face,” he said.
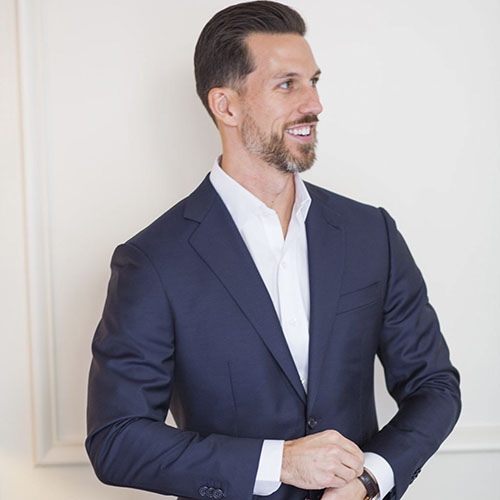
For change to succeed, leaders should help employees understand the importance of adopting what might seem overly novel.
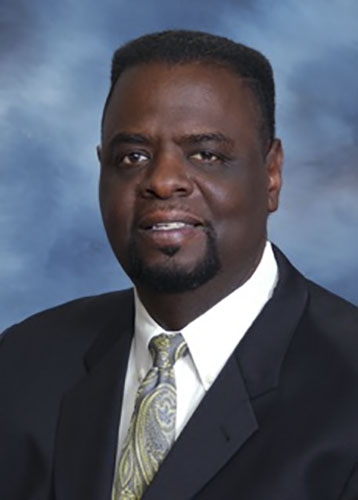
Plant managers who want to ease the pain of change should strive to understand where the real power resides in an organization, Lee continued. Sometimes a certain mechanic on “A” Shift or a particular operator on “B” Shift wields great influence. When they speak it goes viral. “You’ve got to go sit down with them and speak their language,” he said of those informal thought leaders. “A lot of them will sign on if you give them that much respect.”
It pays to integrate a change-management organization into the project team to help bring about the digital transformation, Lee advised. It’s also important to embed the new ways of working into the organization so that change isn’t lost in the long run, he noted. Avoid the “iceberg model” of changing what’s visible above the waterline and leaving what’s below untouched, he said. That can include the attitudes, behavior and beliefs lurking beneath the surface.
The Organizational Help Index can make it easier to assess a plant’s capacity to achieve its stated aspirations, Lee noted. Higher indexes coincide with higher revenue, higher profits and better margins, he said, adding that the index is free and available to all companies.
“If you want to go fast, go alone. If you want to go far, go together.”
Innovatia’s Alex Palmer
quoting an African proverb to describe the importance of helping employees understand digitalization
Ian Klein of Aegex speaking with colleagues in the exhibit hall.
Plants can also refer to the Four-Box Influence Model,
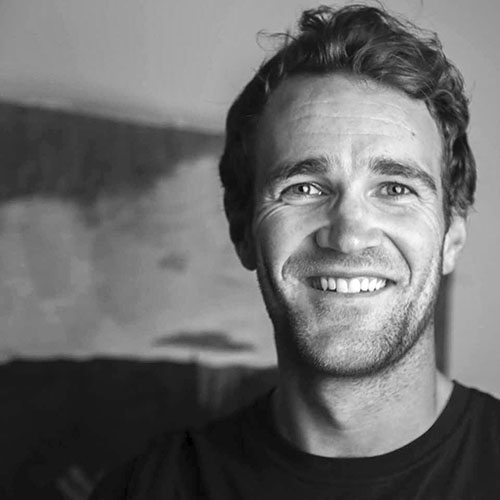
which states that success in change management requires credible, transparent, genuine leadership; a solid business case; training that provides the skills to make the change; and reinforcement of the right behavior, Lee said. Elements that change behavior include helping personnel see the point of change and agree with it; introducing rewards and recognition; and providing good examples at the management level, he concluded.
Focusing on human capital can prove vital to bridging the digital divide, agreed the next speaker to come to the podium, Alex Palmer, Innovatia product manager. Bringing today’s rapid pace of change into an organization becomes a huge undertaking, and “you want to take everyone with you,” he maintained. “If you want to go fast, go alone. If you want to go far, go together.”
But that’s not easily accomplished. Most employees aren’t accustomed to reading thick training manuals, Palmer said. That challenges his company to formalize a clients’ “tribal” knowledge, find the best way to complete a task and then convey that information to users, he noted.
A key element of that knowledge is the realization that unwanted incidents generally occur because of a chain of events – not from a single cause, Palmer continued. It then becomes a matter of “plugging holes” to prevent that unwanted event from happening. “We strive to eliminate information-caused incidents by supplying better information,” he added.
Incidents generally occur because of a chain of events – not from a single cause.
Innovatia helps plants trace problems and often finds that confusion – such as uncertainty about who’s supposed to complete a task – is at the root, Palmer observed. Checklists can help alleviate such situations. It also helps to eliminate vague words like “some” and “if “ from instructions, he noted. Standardization and predictability are important – like avoiding the use of words such as “push” and “press” interchangeably in instructions, he maintained.
If people are doing the same job in four different facilities and each does it differently, it’s worthwhile to find best practices and standardize them as policy, Palmer said. Recording those practices in a structured digital format enables companies to use it on any platform, he noted. “So it’s there to use quickly at the point of need.”
That availability of information is part of the digital transformation that Aegex Technologies wants to help bring about, said the next speaker, Ian Klein, Aegex chief revenue officer. “Digital transformation is one of these inevitable things,” he told the crowd. “It’s like mobility. It’s going to happen.”
Digitalization is occurring as workers take devices like laptops or tablets that are rugged and intrinsically safe into the fields for instant access to technology, Klein continued. Paper and pencil are becoming things of the past, he said. Even though it’s not his company’s core business, it has built accessories – such as hands-free harnesses – that provide employees with access to data and electronic tools while they’re working.
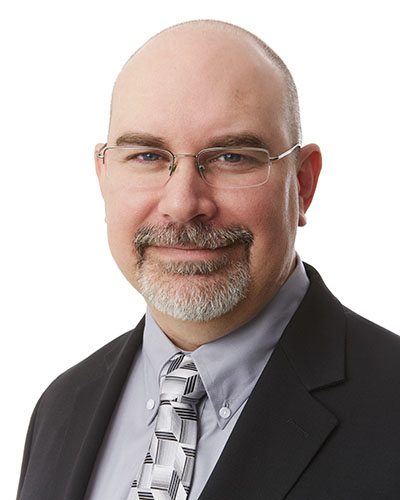
If people are doing the same job in four different facilities and each does it differently, it’s worthwhile to find best practices and standardize.
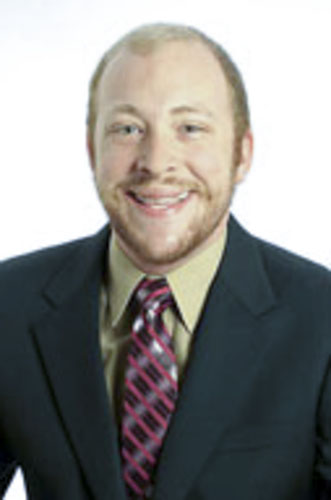
But introducing technology often leads to layoffs, especially among older workers, Klein said. In fact, automation is changing the workplace so fundamentally that some countries are considering a guaranteed wage for displaced workers, he noted. While Baby Boomers may retire instead of face technological change, Millennials expect technology to make data available and won’t stay in a business that doesn’t provide it, he told his audience.
Most people aren’t thinking about the profound effects of change, so getting them ready requires a long process of communication, Klein maintained. “But it’s going to come,” he said of change, “whether it’s in two years or ten years.” And it’s happening in white-collar professions as well as in blue-collar jobs, he said.
It’s a situation where technology always changes but humans never do, agreed the next speaker, Sean Everett, RealWear vice president of business development. But technology merely represents the latest in a series of tools that began with mastering fire and continued through the invention of the hammer, he said. Hammers seemed scary at first, he noted.
Everett then described how his company’s hardhat, which is loaded with technology, can help workers do their jobs and document their progress with the assistance of data and tools. “We can potentially make someone’s job easier,” he said. New employees can use the device to create a record of what they’re doing for review by senior colleagues, helping to reduce the fear that arises when performing unfamiliar tasks. That makes the device an aid in the effort to manage the digital divide, the subject of the session.