Total Solutions
Optimize design, fabrication, and installation through Koch-Glitsch ONE-SOURCE SOLUTION
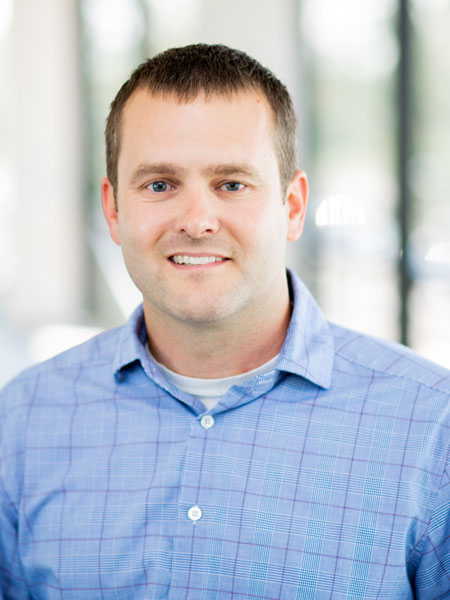
When you walk into the Koch Engineered Solutions (KES) booth, they’re not going to sell you a product. “We ask our customers what they are trying to accomplish,” says Billy Unruh, Senior Business Director (Koch-Glitsch/Koch Heat Transfer Americas) at Koch Engineered Solutions . “We partner with our customers and really dig into their problems and opportunities. We can help with whatever that may be—reduced energy consumption, increased capacity and/or efficiency, lower input costs, mechanical upgrade, speed in delivery, installation expertise, and total plant solutions.
KES provides unique solutions in construction; mass and heat transfer; combustion and emissions controls; full engineering, procurement, & construction; utility-scale solar. It offers global engineering and sales offices, research and development, manufacturing facilities, comprehensive aftermarket support, and more than 8,500 employees, with 6,000 based in the Americas, to meet the needs of customers.
Safety is a key focus at KES: Act with proper regard for the rights of others, put safety first, drive environmental excellence, and comply with all laws and regulations. Stop, think, and ask.
“If you’ve ever come to a Koch facility, not only would you see it right away with signage, but you would see it in our actions. It is who we are.” says Unruh. “We understand that to drive the best outcomes, we must create mutual benefit, and if people aren’t in a safe environment, they’re not going to seek ways to transform what they do and how they do it. Koch Engineered Solutions promotes a culture where each person is seeking advancements within safety, sustainability, and operational excellence. A specific focus is material utilization. As we reduce the material usage in our equipment, we’re responsibly using fewer resources and providing greater outcomes. It also helps us reduce our cost basis and allows us to provide products to the industry at a better price point, while also driving sustainability.”
You will see that you can run the process as you did it for the last 50 years or you can use new technologies and you can easily save 30% on energy
—Robin Schulz, Global Technology Leader in Specialty Separations, Koch Engineered Solutions
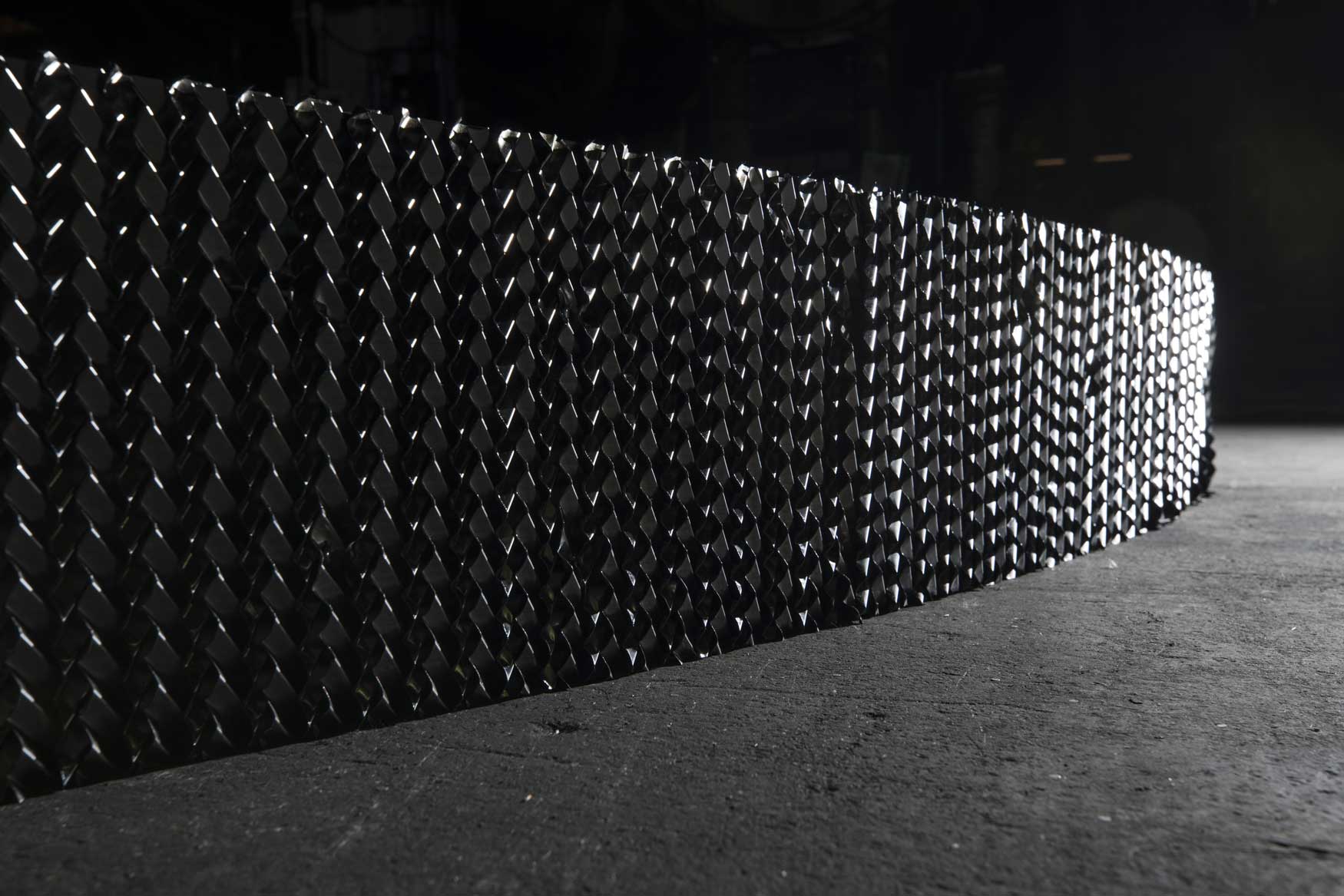
PROFLUX® Severe Service Grid: The high-performance severe service grid packing from Koch-Glitsch combines the efficiency of structured packing with the robustness and fouling resistance of grid packing.
KES is sponsoring two seminars that focus on energy efficiency, both presented by Robin Schulz, Global Technology Leader in Specialty Separations at Koch Engineered Solutions. “You will see that you can run the process as you did it for the last 50 years or you can use new technologies and you can easily save 30% on energy. And it’s not science fiction —it’s available, it’s industrial-scale proven technologies—but many are not aware of the advancements or are not comfortable using them, and we want to address that here,” says Schulz.
Schulz will first present “Vacuum Distillation Optimizing Separation.” Vacuum distillation often requires special equipment to perform, unlike atmospheric or high-pressure distillation applications. Therefore, wire gauze structured packings with low liquid load distributors are often used. Ensuring a holistic design of these two components is essential to obtain the optimum ratio between pressure drop and separation efficiency.
In many plants, there are towers not running in optimal conditions. To overcome this, operators must increase energy demand; it’s the only option they have. Schulz will demonstrate that putting structured packing together with the liquid distributor will cause a temperature drop, which means capacity at the end and separation efficiency. It’s possible to separate very temperature-sensitive substances with minimum energy demand.
Schulz will then lead a second seminar, “Dividing Wall Columns.” Dividing wall columns are a proven technology that saves a considerable amount of energy, but even today, opinion persists that they are a fringe application in distillation and that the mechanical challenges are too great to bring dividing wall columns to a wider range of applications.
“In a typical column sequence, you operate the first column to separate the first product and then the second column to separate the second product, which requires a lot of energy,” says Schulz. “Or you can put both separations in one column so you can use the energy for both separations, which will save 30 to 50% of energy.”
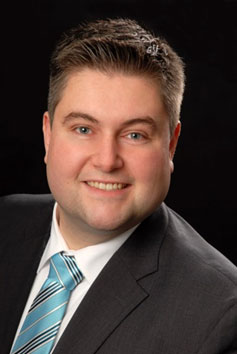
We want to convince the engineers that this is really a proven technology, it’s not science fiction.
—Robin Schulz, Global Technology Leader in Specialty Separations, Koch Engineered Solutions
Optimize design, fabrication, and installation through Koch-Glitsch ONE-SOURCE SOLUTION
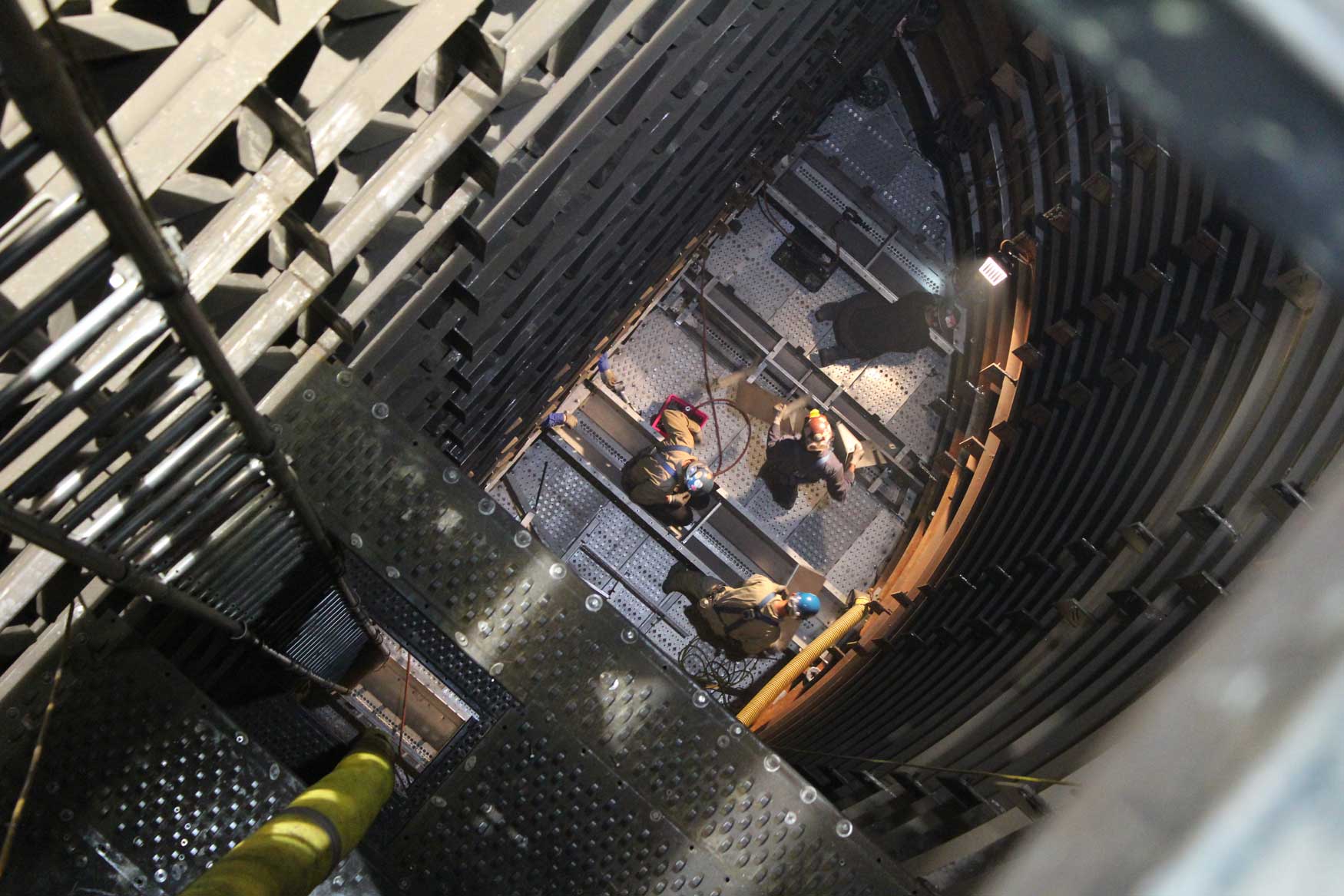
Koch-Glitsch tray installation completed by Koch Specialty Plant Services
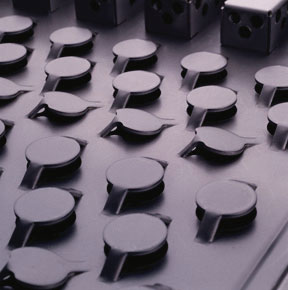
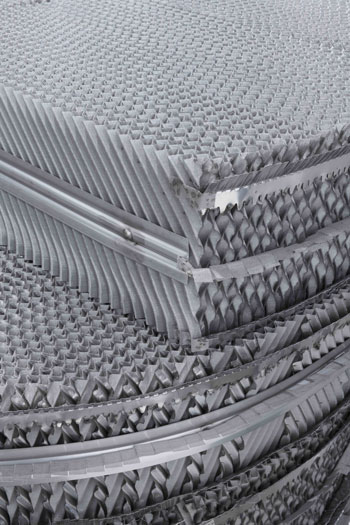
“So, the first one was in operation 40 years ago? In the meantime, there are hundreds of divided wall columns, but in the U.S., it’s still not very common,” says Schulz. “Of course, energy was not so expensive in the past. But we see more and more companies are interested in this technology because the plants are smaller. You save room, you save a lot of investment costs, let’s estimate between 15 to 30%. And you save a lot of energy, 30 up to 50% for these distillation separations. We want to convince the engineers that this is really a proven technology, it’s not science fiction. If you have the first one, you will really understand that this is the right technology, and the next 10 will directly come.”
Zack Bondley, global technology leader in packing at Koch-Glitsch, will present a seminar titled “Applying Carbon Capture Technologies.” Post-combustion carbon capture is a vital technology in the future of energy as we strive for decarbonization. Koch Engineered Solutions can leverage a wide range of capabilities designed to help customers achieve their goals. Structured packing and properly engineered packed tower internals are utilized together to handle the unique requirements for amine-based post-combustion carbon capture technologies by providing an optimal combination of efficiency and low pressure drop. Koch-Glitsch’s R&D carbon capture facility allows for testing of a variety of point-source CO2 compositions with our structured packings to ensure a superior design for these units. This optimization helps to reduce the capital and energy requirements of full-scale carbon capture facilities. This presentation shows the capabilities that Koch Engineered Solutions has available and shows the application of structured packing technology for post-combustion carbon capture units.
Koch Engineered Solutions is an integrated company and will showcase a wide variety of products, services, and solutions at its booth, including EPC services through Optimized Process Design (OPD), mass transfer through Koch-Glitsch, combustion through John Zink Hamworthy Combustion, and installation services through Koch Specialty Plant Services (KSPS).
“We’re not looking to push a specific solution. We’re looking to partner to develop the best solutions,” says Unruh. “We love to solve problems, and we’re looking to partner with our customers to find solutions.”