How to Quench an Arc Flash
Put safety first and increase uptime.
An arc flash can reach temperatures up to 35,000 degrees Fahrenheit—hotter than the surface of the sun—causing significant equipment damage, downtime and potential injury. Fortunately, installing the right equipment can enhance safety for personnel and reduce the risk of significant downtime for operations by protecting equipment from damage.
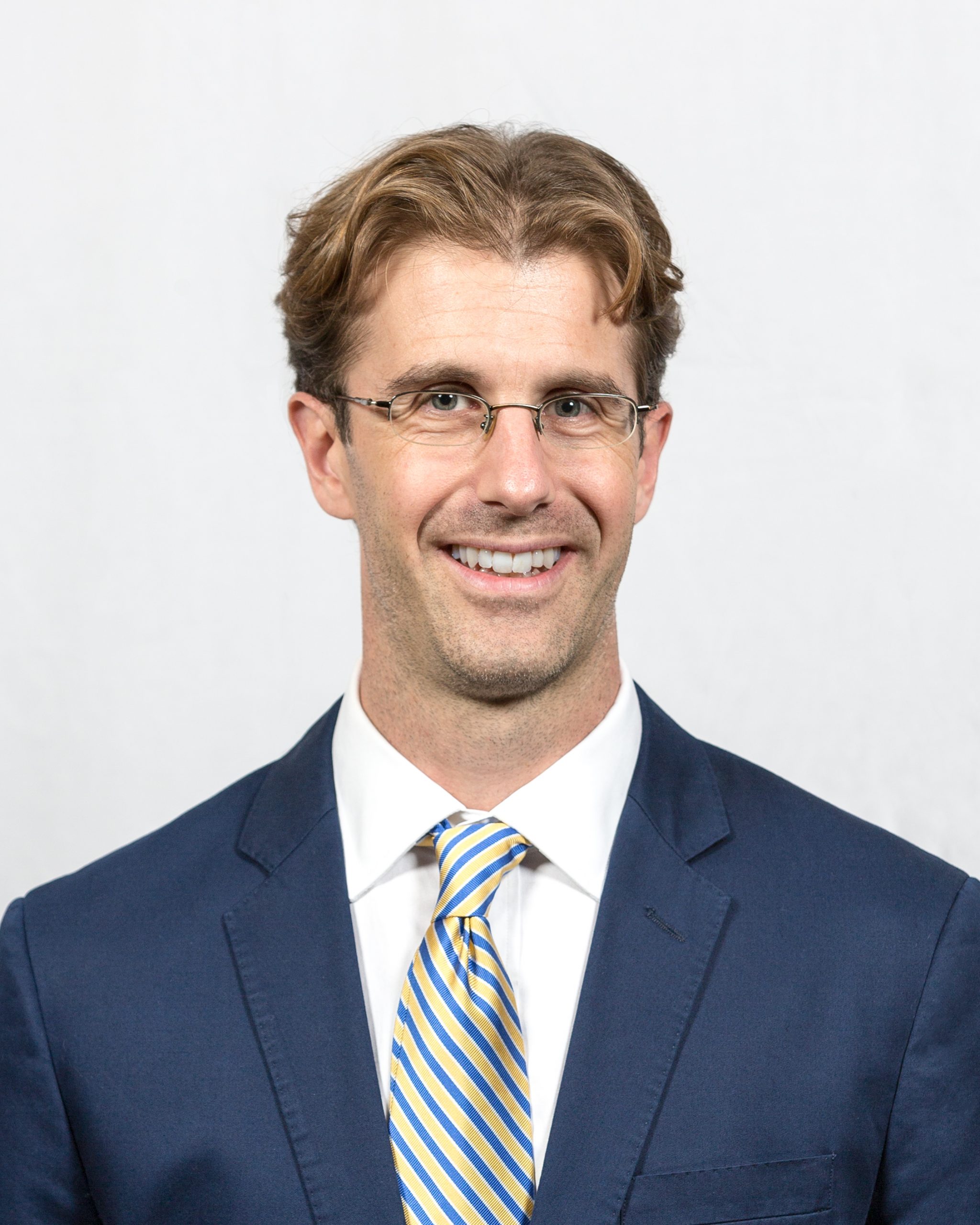
The drop of a tool or accidental contact with an energized conductor can cause an arc flash event. The temperature from an arc flash can reach upwards of 35,000 degrees Fahrenheit—hotter than the surface of the sun. Fortunately, installing the right equipment can enhance safety for personnel and reduce the risk of significant downtime for operations by protecting equipment from damage.
Eaton is returning to eChem Expo in 2020 to emphasize solutions enhancing safety and uptime for critical process industries. Eaton is a power management company dedicated to helping customers effectively manage electric, hydraulic, and mechanical power more efficiently, safely, and sustainably. Worldwide they have approximately 101,000 employees with customers in over 175 countries.
“Electricity is supposed to flow through a designated conductor, like a copper wire,” explains Adams Baker, Product Manager at Eaton. “When there is a fault, electricity may instead flow through the air between phases of opposite polarity or from phase to the ground. When that happens, you can have an arc flash event, which releases lots of energy. Current is essentially jumping through the air from phase to phase or phase to ground, whichwill cause the conductors to melt, vaporize, and then ionize. When any element transforms from solid to gas, it expands. For example, copper expands by 67,000 times. The energy can cause equipment to be destroyed.”
“The more energetic the arc flash, the more dangerous it is and the more damage can occur to the equipment. Yet, recent innovations enable electrical equipment to withstand an arc flash event with little to no damage.”
Recent innovations have dramatically reduced incident energy so that equipment can withstand an arc flash event with little to no damage.
Adams Baker, Product Manager, Eaton
Eaton’s Arc Quenching Switchgear supplies power to a new production line for AGC Glass North America, enhancing electrical safety and uptime.
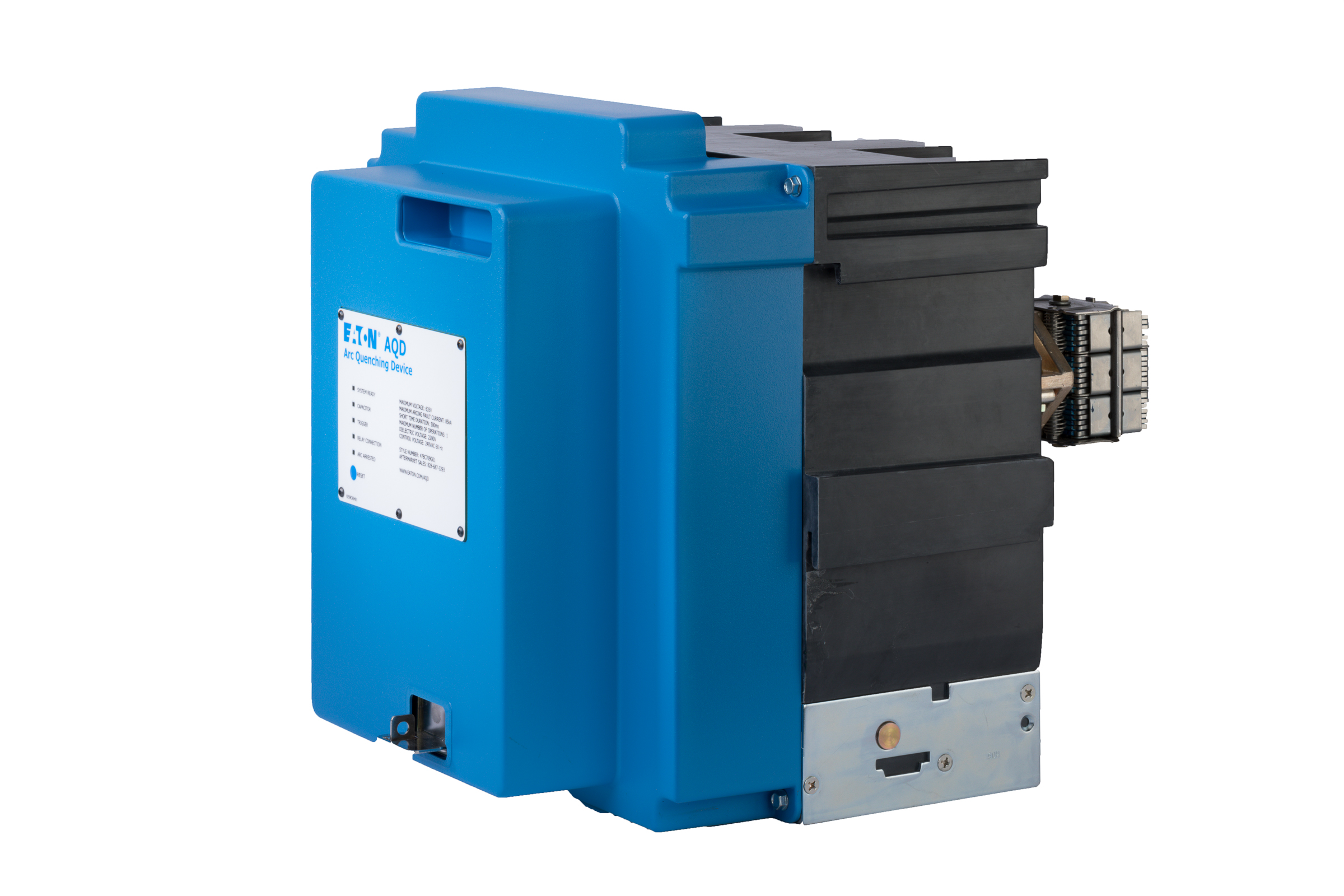
Safety is the first priority. Downtime is also especially urgent for continuous process industries. Without the right equipment to mitigate an arc flash, there can be substantial impact to both personnel and operations from a single event.
“Typically, there are two ways that the chemical industry can deal with arc flash events,” explains Baker. “Organizations can reduce the intensity or contain the energy. There are a variety of solutions to reduce arc flash energy. For example, Arcflash Reduction Maintenance Systems can detect a fault and clear it using an upstream circuit breaker. In addition, there is arc-resistant equipment available that is designed to contain an arc flash event and redirect energy away from personnel.” Arc Quenching Switchgear leverages the former method, reducing the intensity of an arc flash, but in a revolutionary way.
Eaton is building on expertise in electrical power systems, and decades of industry-first solutions designed to reduce the likelihood of an arc flash event. Eaton developed industry-first technology. “Eaton’s Arc Quenching Switchgear extinguishes the arc flash in less than four milliseconds, greatly reduces potential impact and damage from the arc flash event,” Baker says.
On the tradeshow floor, Eaton will showcase Arc Quenching Switchgear that’s capable of operating ten times faster than solutions that rely on tripping a circuit breaker to interrupt an arc fault. “So that means an flash exists in the equipment for a tenth of the time or less––thus preserving the equipment and reducing downtime,” says Baker.
At eChemExpo, Baker will also present a case study featuring AGC Glass North America, the world’s largest glass manufacturer. “AGC Glass selected Eaton’s Arc Quenching Magnum DS low-voltage switchgear because the technology best met their safety and reliability requirements.
Stakeholders in electrical safety and plant uptime should attend to learn more about how to reduce the impact of arc flash events. A second seminar by Eaton will discuss changes to IEEE 1584 and how they affect arc flash studies. This session is important for anyone responsible for safety and maintenance at their facilities.
Eaton has taken the lead in electrical solutions addressing safety and uptime. “With the continued evolution of the internet of things and the connections to the cloud,” says Baker, “we can leverage the data in the cloud to perform predictive diagnostics to anticipate when equipment needs to be serviced or predict an imminent failure before it occurs versus doing preventative maintenance.”