The new Centre for Flow Processing will be the focal point for integration of commercial, research and university educational activities.
The reality of reducing energy consumption with heat transfer solutions.
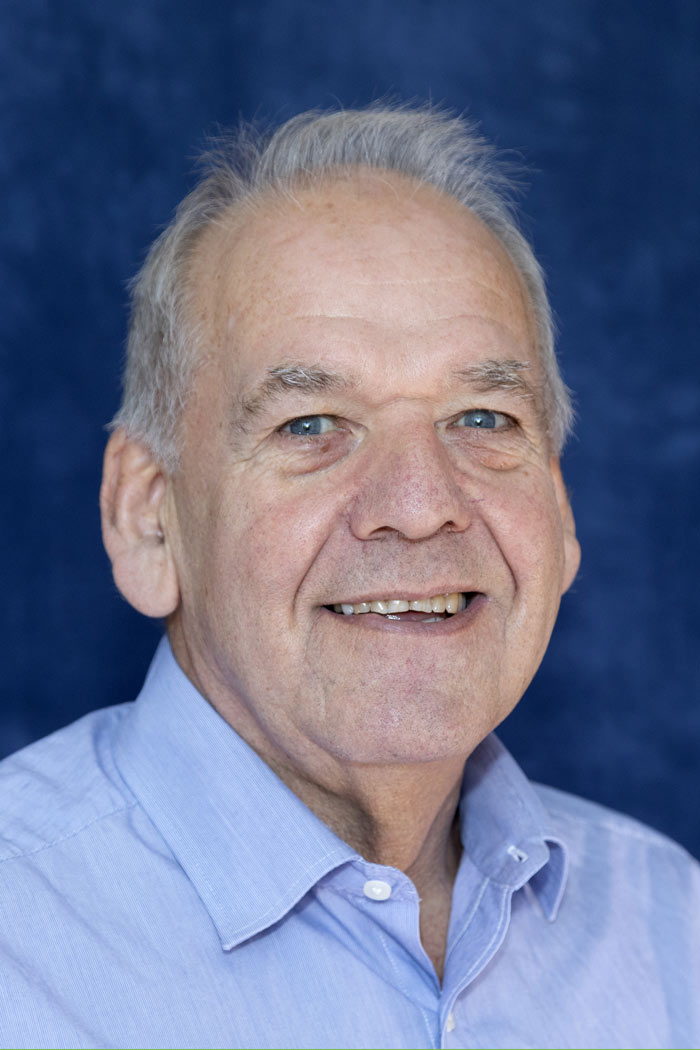
The reality of reducing energy consumption with heat transfer solutions.
At a large conference with 1,800 delegates last year, CALGAVIN Ltd., founder and Managing Director Martin Gough asked a simple question: “Is there anybody here in the room whose job title is energy reduction manager?”
Silence from the audience.
“Does anybody know of anybody who is an energy reduction manager?” Gough continued.
Still no answer.
“Okay. Can I assume, then, that energy reduction is really not a very important thing for plants?” asked Gough.
It’s time to get serious about energy reduction.
The fact is that energy reduction should be important to all process plants.
CALGAVIN Ltd. was founded by Martin Gough in 1980. The company partners with some of the largest global businesses to provide robust heat transfer solutions to the process industries. They have about 40 employees and are based in Warwickshire in the United Kingdom. As for the business, Martin could see the processing need and was eager to start his own business, so he bought an off-the-shelf company, Cal Gavin, which has grown its technology to worldwide recognition over four decades.
Today there are more than 20,000 exchanges worldwide with CALGAVIN products inside them. They currently manufacture between three to five miles of product a day that is delivered to plants around the world. The company is built on its high-integrity research facility, generating data that is available via it’s DLL in exchanger design programmes provided by AspenTech, HTRI and CALGAVIN licenses. Whilst these powerful enhancement products are not actually visible, their integrity and performance can be relied upon through their rigorous testing procedures and, process warranties.
Gough was recently asked to advise on an energy reduction strategy for a large company in the Middle East. “Previously, the plant operators have never had to look at energy reduction and certainly not across whole plants, as crude oil is so cheap when valued point of extraction before being traded”.
“Influenced by the pressures from global warming, the head of the country decreed that it’s production companies must substantially reduce their energy (CO2) emissions, a requirement that is an almost impossible sudden challenge and unconsidered previously. Global warming is challenging the world!
The planning, engineering, and implementation of carrying out energy reduction projects is not established within most companies. There is a fundamental resistance to change anything on plants operating under license that risks plant integrity and above all that might risk its profitability in any way. If you alter the process and something goes wrong, you’re in trouble. So, in a sense, they are faced with approaching something they have never had to do before or fund but they have to do it now, and so we have skills and experience to help them.
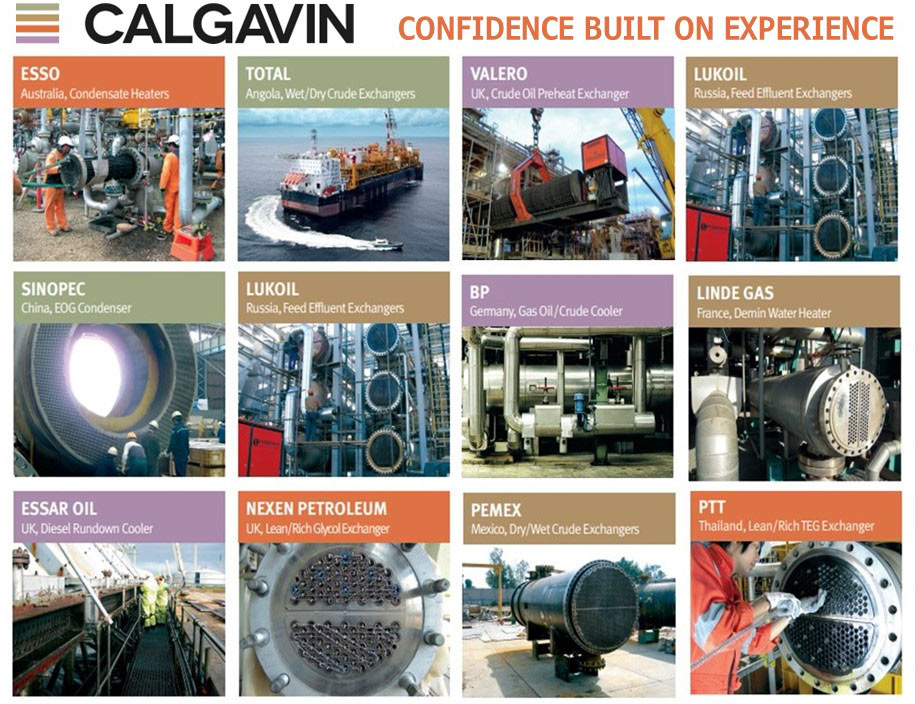
Then suddenly the head of the country decreed that it’s production companies must substantially reduce their energy emissions, a requirement that is an almost impossible challenge and unconsidered need previously. Global warming is challenging the world.
— Martin Gough, Founder and Managing Director, CALGAVIN Ltd.
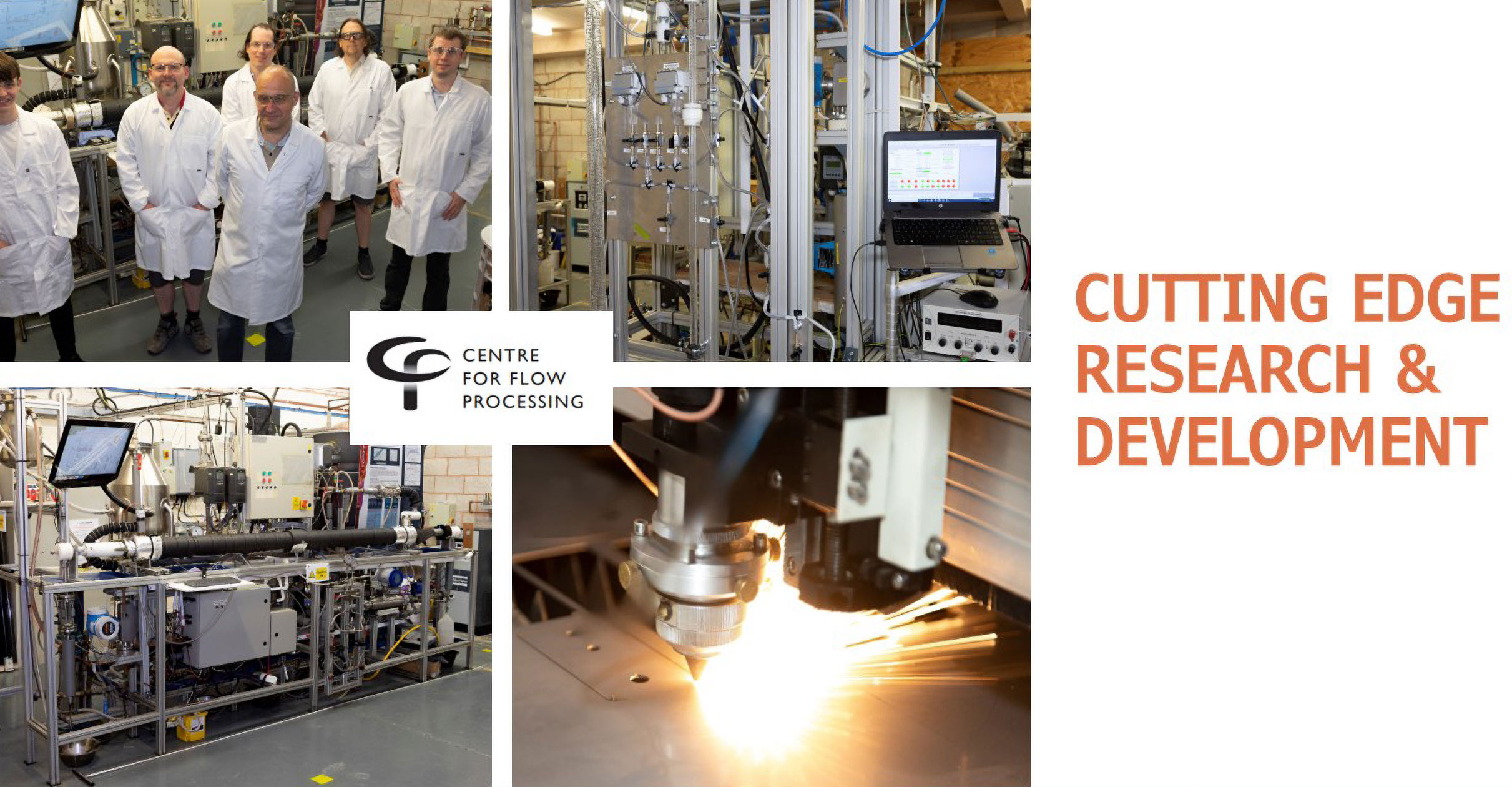
Gough says thermal process integration is an excellent tool for optimising energy use on new plants where exchanger layout and thermal paths can be optimised for minimum energy use.
It has limited value though, in applying it to existing plants where exchangers are in fixed positions, can’t be shuffled around and there’s usually no space to add new exchangers anyway. Modifying pipe layouts on an existing plant to incorporate more exchangers is seen as an unwelcome attack on the integrity of the existing process design and can easily be more expensive than the value of the energy being recovered.
There are strategies though to reduce energy usage in some types of plant and equipment. Companies do not want to pay for energy reduction, unless it can be shown to have a good return on investment. These opportunities are akin to low-hanging fruit—easily attainable targets that plants should prioritise. CALGAVIN only proposes changes that they can accurately predict and guarantee. The expertise and experience needed to identify these energy-saving opportunities are often absent within the internal resources of most operating plants.
CALGAVIN originally developed, hiTRAN Thermal Systems, a wire matrix element (turbulators), made up of diameters of 6 mm to 100 mm that go in tubular heat exchangers and reactors. CALGAVIN also manufactures twisted tapes, mostly used in repeat business of existing designs and for quite limited applications. These, hiTRAN Systems and new products specifically dealing with the challenges of high viscosity in the range of 1.0 to 40 Pascal Seconds will be on display at the trade show.
“Many process companies don’t now have the capacity for research and new product design, most outsource wherever possible,” says Gough. To meet this gap, CALGAVIN is founding the Centre of Flow Processing, a 32,000-square-foot facility, to do both fundamental and applied research to meet client needs when developing new processes. The Centre will build on Gough’s 40-year relationship with the School of Chemical Engineering, the University of Birmingham together with other universities and research institutions. CALGAVIN will provide for the training and work experience for university engineering students.
Whilst the world is obliged to continue to use fossil fuels all efforts should be made to use alternative sources of energy. There remains a fundamental conflict though between the enormous global revenue made by governments and large corporate institutions controlling oil and gas and having an unstoppable momentum, slowing down the drive and implementation of renewables. “We aren’t going to get away from fossil fuel for years yet because full replacement is nowhere near ready and remember, it’s really all about the money!”
We aren’t going to get away from fossil fuel for years yet because full replacement is nowhere near ready and remember, it’s really all about the money!
— Martin Gough, Founder and Managing Director, CALGAVIN Ltd.
Whilst we are moving away from oil and gas, there are still substantial opportunities to reduce energy usage on existing processing plants. CALGAVIN is a unique company that can offer technology and experience in studying and improving the performance of heat exchangers and reactors providing tangible benefits to increasing production and reducing energy consumption.
Martin Gough, Managing Director, will present “Optimising Chemical Process Efficiency Through Enhanced Heat Recovery.” Optimization of heat exchangers for efficient heat recovery in thermal processes is an important aspect to reach net zero goals. Attendees will learn how the use of hiTRAN Thermal Systems in such designs, with up to 16 times higher tube side heat transfer, leads to compact units with improved operability.
“Heat Transfer Enhancement for Greater Efficiency in Tube Side Multicomponent Condensation Design” will be presented by Nathan Hill, CALGAVIN Technical Sales Engineer. The use of hiTRAN Thermal System (heat transfer enhancement technology) improves several aspects of tube side multicomponent condensation processes. Attendees will learn the limitations of conventional multicomponent condenser design with large amounts of non-condensable and the significance of heat release curves to characterize condensing processes.
“There are thousands of plants around the world that are not going to be replaced,” says Gough. “We need to make them as efficient as we can.
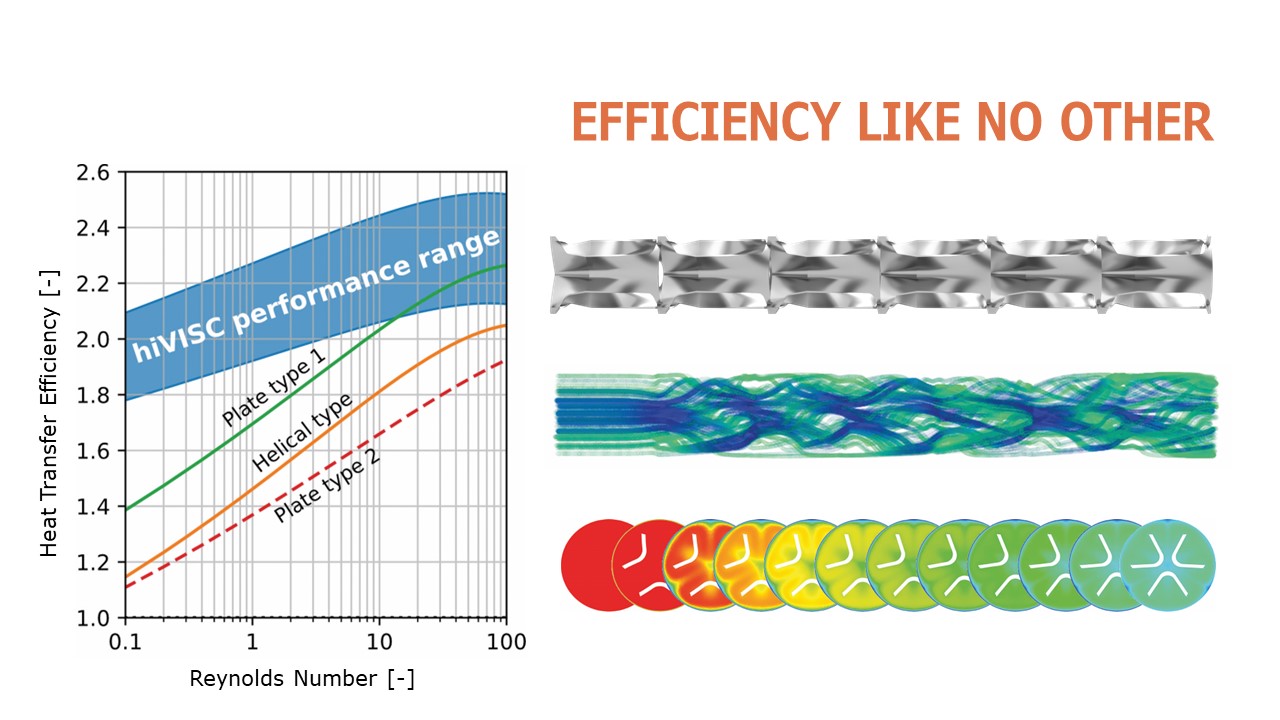
