Preventing Disaster
Technology Extinguishes an Arcing Fault Before It Runs Wild
A chemical plant can become a living nightmare within milliseconds when electrical current leaves its intended path inside a piece of equipment and begins arcing through the air. “It’s almost like a bomb going off inside of the switchgear,” says Chris Finen, an Eaton Corp. PLC senior application engineer.
In a confined space, the arc superheats the air and builds tremendous pressure. It can vaporize metal, throw off a fireball, hurl hot shrapnel, and blow open doors and panels. The heat and fire can severely burn workers unfortunate enough to be nearby, while the sound wave can pierce eardrums and the flash of light can singe retinas.
Production can stall for weeks or even months while the plant repairs or replaces equipment. So losses become threefold. Besides the tragedy of personal injury and the unwelcome cost of restoring the plant’s operating capacity, there’s the unrealized value of unproduced goods.
The key to preventing that devastation is to interrupt the internal arcing fault quickly enough to avoid reaching the peak of the pressure wave, and a “major breakthrough” from Eaton does exactly that, according to Finen. Eaton’s new Arc Quenching Switchgear, or AQS, detects and extinguishes electrical arcing faults in less than 4 milliseconds –dramatically reducing the hazard, he says. Production can often resume in a matter of hours, he adds.
The AQS “reacts 10 times faster than systems that rely only on circuit breakers, does not affect system coordination, and is effective even with doors open, covers removed, or breakers racked out,” Finen continues. At the heart of the AQS is the Arc Quenching Device, or AQD. It extinguishes arcing faults by creating a lower-impedance path through the AQD, he says.
The key to preventing devastation is to interrupt the internal arcing fault quickly enough to avoid reaching the peak of the pressure wave.
That’s accomplished without creating a bolted-system fault, which would put enormous stress on the upstream distribution system, Finen notes. Peak currents during the quenching of an arcing event are at least 25 percent lower than the prospective bolted-fault currents, he says.
The protection comes without the need for users to intervene or engage a maintenance mode, Finen maintains. The system always remains active, regardless of the state of the switchgear. It also continuously monitors the health of the system, and it’s fully testable during periodic maintenance intervals.
Other competing arc flash reduction techniques rely on circuit breakers to interrupt the arcing event, Finen says. That approach is too slow to prevent the peak pressure wave from forming inside the gear and causing a series of hazardous conditions and significant equipment damage, he contends.
Competing arc resistance switchgear systems may protect workers if all of the enclosure’s doors are closed and latched, covers are in place and breakers are in their cassettes, Finen says. But Eaton’s AQS remains effective even when operators open doors or panels for maintenance. “So it’s a significant safety advance,” he says.
“It’s almost like a bomb going off inside of the switchgear.”
Chris Finen
an Eaton Corp. PLC senior application engineer, describing an internal arcing fault
This diagram shows the steps that an Eaton Arc Quenching Device takes to detect and extinguish an arcing fault before it can wreak havoc in a plant.
With competing systems,
beefing up the walls of an enclosure and strengthening the latches aren’t enough to protect workers who have to open door or panels to perform maintenance, Finen notes. “All bets are off and you no longer have arc protection,” he says of traditional arc resistant switchgear systems during maintenance.
Eaton began marketing and taking orders for the new AQS in the third quarter of last year and plans to begin shipping it to customers this year, Finen says, adding that the technology represents the results of many years of research, development and testing.
Discussion of the new AQS is expected to fuel one of the two Eaton presentations at eChem Expo, Finen says. Likely attendees at those sessions could include power system engineers, maintenance engineers, consulting engineers, electrical maintenance personnel and plant engineers.
In its other eChem Expo session, Eaton plans to discuss the company’s Vacuum Fault Interrupting transformers. The VFI transformers combine a vacuum interrupter with a standard pad-mount or substation-type liquid transformer. The devices provide not only primary protection for the transformer but can also reduce the arc flash risk on the secondary of the transformer and for downstream switchgear, Finen says.
Eaton offers a VFI transformer package that combines transformer protection and arc flash reduction into a single combined package, Finen maintains. It optimizes footprint, reduces installation time, and improves system and personnel protection, he says. VFI transformers can be of deadfront construction with external gauges and controls all designed to minimize exposure and the likelihood of having an electrical safety incident.
Beefing up the walls of an enclosure and strengthening the latches aren’t enough to protect workers who have to open door or panels to perform maintenance.
VFI transformers have been available for more than 15 years and include proven vacuum protection technology, Finen says. However, Eaton is now highlighting applications that use the technology to reduce arc flash and improve worker safety, he notes.
It’s the result of decades of research and refinement of vacuum interrupter-based technology used in vacuum reclosers, vacuum circuit breakers and other applications, Finen notes. Eaton can provide VFI transformers with Envirotemp FR3 insulating fluid, a seed-based oil that’s more environmentally friendly and safer than the mineral oil that’s often used, he says.
Other Eaton products help manage electrical, hydraulic and mechanical power, Finen continues. Examples include safety products and services that relate to electrical power, such as circuit breakers, fuses and protective relay devices, he says, adding that, “all enhance electrical system safety and reliability.”
Eaton ties together data through connectivity and the internet of things, Finen says. He provides the example of the Power Xpert Dashboard – a data visualization tool for a switchgear that can be mounted a safe distance away from the gear to pull together advanced information from all of the devices and aggregates it on one intuitive touchscreen that a user can also access on a tablet or smartphone.
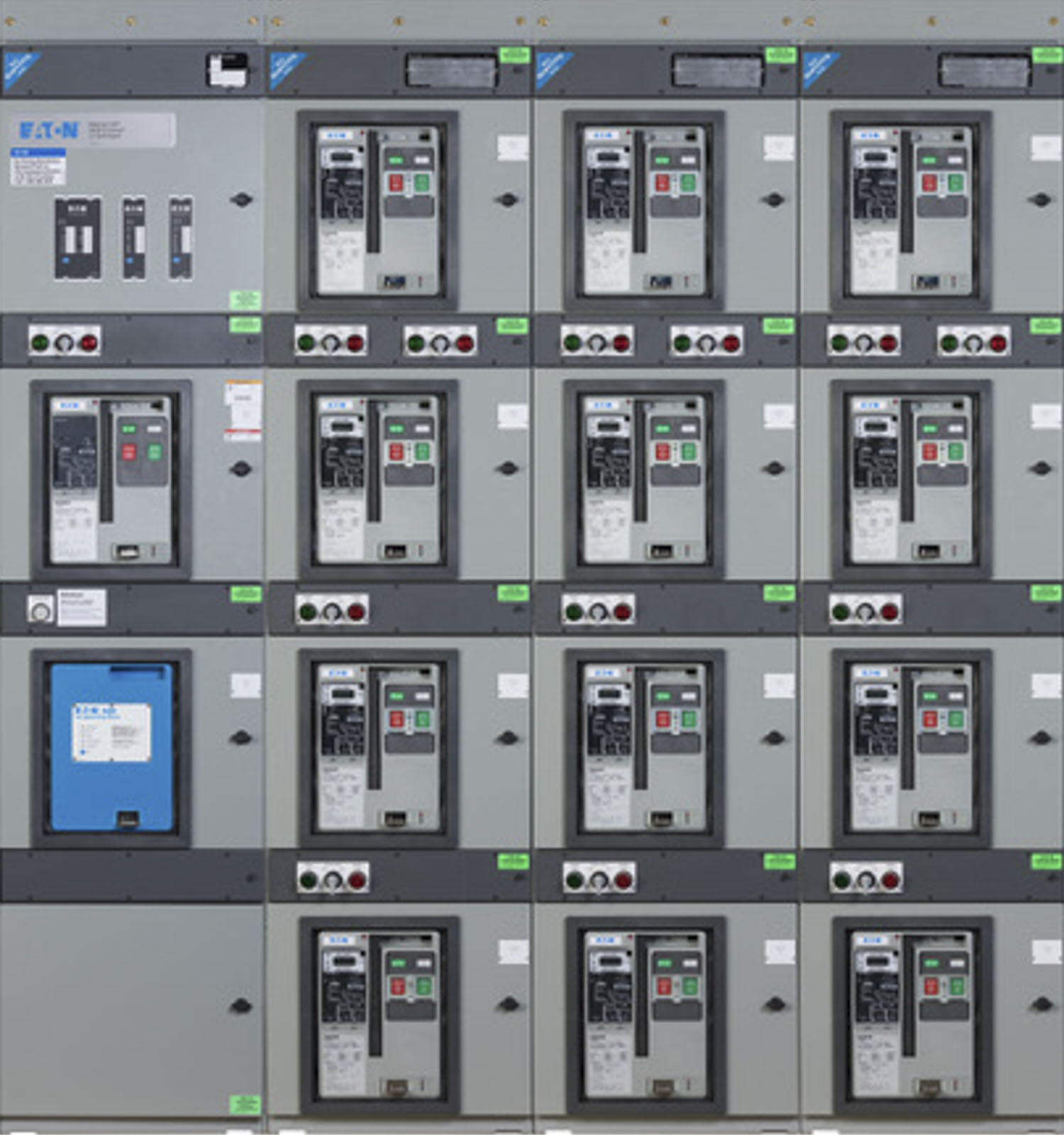
Improvements in monitoring and diagnostics will empower management and operators with information that helps them understand the health of their plants and head off problems before they cause unplanned downtime.
The dashboard shows alarms, trends, arc flash risk and the level of personal protective equipment needed based on the current condition of the gear, Finen notes. It’s focused information available in the safety of an office and relevant to the task at hand – not just lots of data, he says.
Whether it’s a dashboard, VFI, AQS or another Eaton product, more than 1,000 people in the company’s Engineering Services and Systems Division work directly with customers for the life of the equipment, Finen says. Eaton provides help with maintenance, testing, training and life-extension services for all of its distribution products, he notes.
And there’s history and scope to back those claims. Eaton Corp. PLC grew out of a company formed in New Jersey more than 100 years ago, and it now maintains operational headquarters in suburban Cleveland. The company employs more than 96,000 people worldwide and does business in 175 countries.
Looking to the future, Finen predicts that Eaton will continue to develop technology that enhances safety and reliability of electrical systems. Improvements in monitoring and diagnostics will empower management and operators with information that helps them understand the health of their plants and head off problems before they cause unplanned downtime, he says.
In the future, the packaging of the Eaton’s systems will change, reducing the electrical infrastructure’s footprint, Finen continues. Doing the same thing in less space leaves more room for income-generating activities, he notes.