Peace of Mind for Your Plant
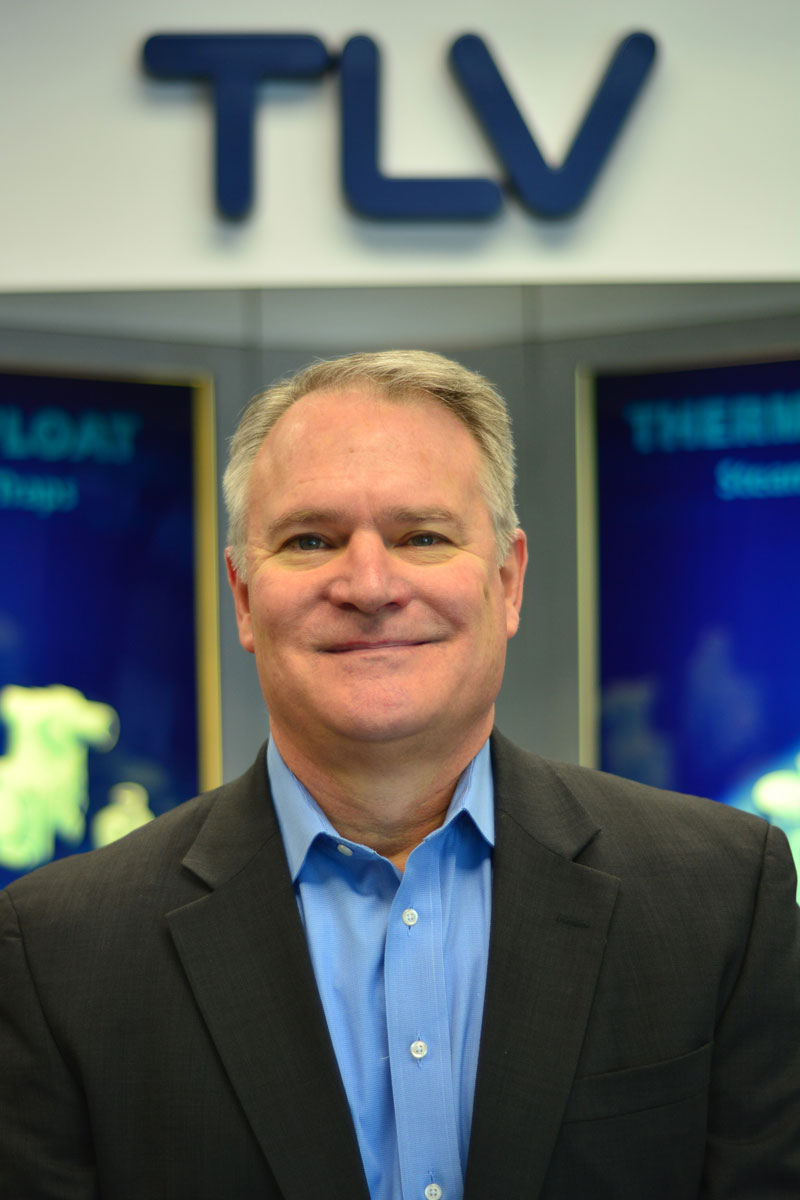
So you need to make sure you don’t have off-spec steam. Optimizing your steam supply operation to deliver that heat to your plant and your processes is critical.
“At TLV, our approach with our customers is not to talk about our products,” says Norm White, President of TLV Corporation, the U.S. subsidiary of TLV. “We want our customers to think about systems: their steam system, their steam heating applications, and where they’re using steam as a motive, in a flare or a turbine, and condensate recovery. We’ll help them optimize those systems and run them safely.”
Established in Japan in 1950, TLV has grown to become a world authority in steam engineering products and services. TLV now counts companies in 13 different countries and offers products through over a hundred distributors worldwide.
We created SSRM, the world’s first service for quantifying and mitigating risk to steam systems.
—Norm White, President, TLV Corporation
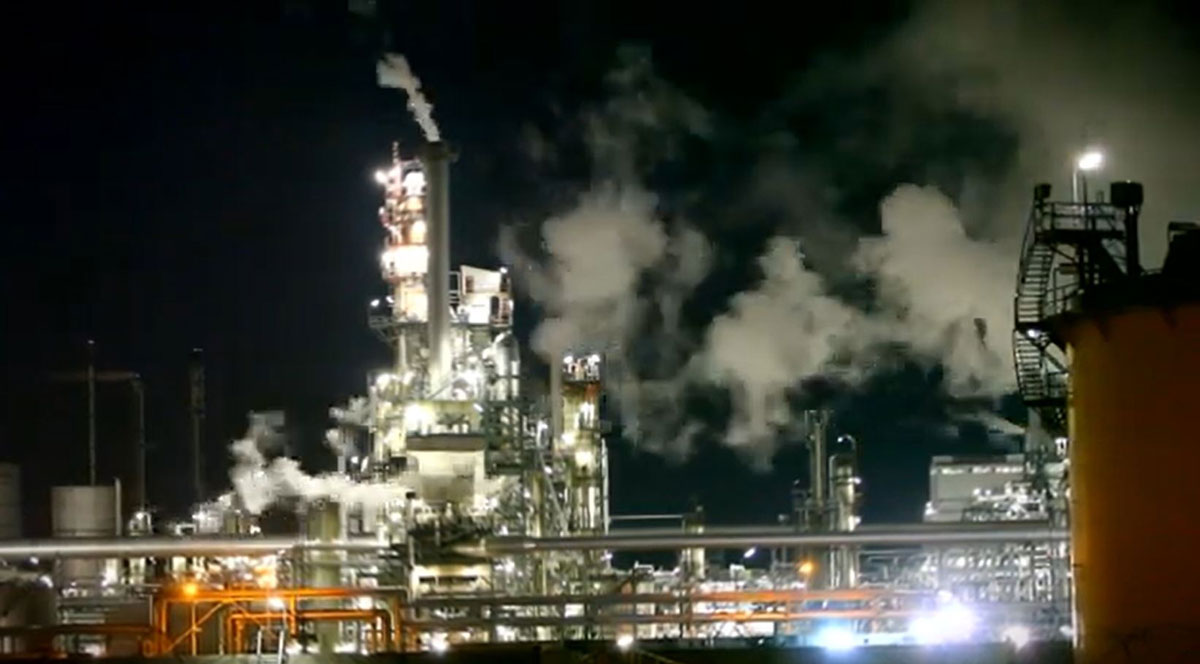
“Utilizing our steam engineering know-how and extensive experience with inspecting and optimizing steam traps and related steam equipment, we created SSRM, the world’s first service for quantifying and mitigating risk to steam systems,” says Norm. “With limited resources, it is not possible to pursue all actions. But it’s realistic to implement only where the need is greatest.”
A risk matrix visualizes clearly how much risk each piece of equipment is currently exposed to and makes it easy to prioritize which equipment should be handled first. The effect of potential mitigation actions can be simulated using the same methodology. These simulations make it possible to determine in advance which mitigation action will be the most effective. The accuracy of the risk analysis is derived from the TLV’s expertise from more than 70 years of mitigating the risks faced by steam systems.
“TLV is the only company that brings that steam know-how and experience together with that risk mitigation software piece,” says White. “We’re unique in this area.”
“For the last 10 years, we’ve been developing a risk-based inspection process for steam assets, and we’re the only company in the industry that has done so,” says White. “We have been using that same methodology and applying that to steam assets, and now the industry is adopting it as part of the API 581 guidelines to make it standard.”
TLV also helps plants achieve greater sustainability without heavy capital investment. “When most people think about decarbonization, they’re talking about impressive transformational things that are going on in the industry. But many of these innovations require heavy capital investment and the time to implement those solutions,” says White. “TLV offers customers the opportunity to be proactive with their steam system to help them with their energy efficiency. For every 1,000 pounds of steam that we can save from being wasted or leaked from their system, typically, that will correlate to a reduction of 150 to 180 pounds in CO2 Emissions. So, if we’re able to repair steam traps and the customer is saving 100,000 pounds—which is very possible in an entire petrochemical complex—we’re looking at a reduction of 150 to 180 pounds in CO2 emissions. That savings is something we can contribute to both energy efficiency and reduction.”
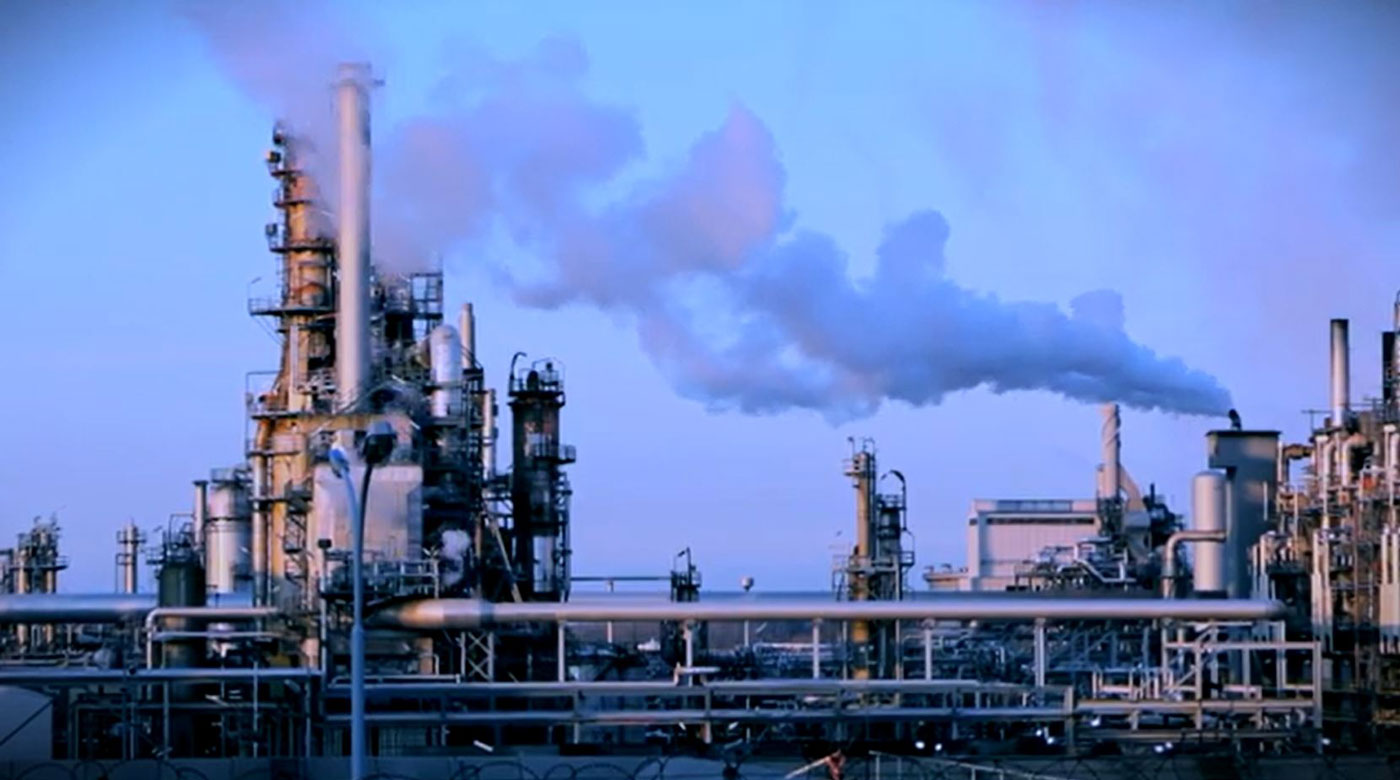
Discover the fundamentals of achieving optimized heat transfer and complete condensate drainage and recovery in a seminar hosted by TLV.
Alec Newell, Consulting Supervisor, TLV Corporation, will lead a seminar, “Best Practices for Steam-Heated Jacketed Vessels and Reactors.” No two jacketed vessels or reactors are the same. The infinite combination of jacket and piping configurations makes standardization of steam supply and condensate drainage piping a challenge. The difficulty can be compounded when the same jackets are used for and cycled between steam heating and water cooling. Water hammer and poor performance often result, leading to process inefficiencies and maintenance headaches.
This presentation will explore some of the design and operating pitfalls that can arise with steam jackets and discuss the fundamentals of achieving optimized heat transfer and complete condensate drainage and recovery.
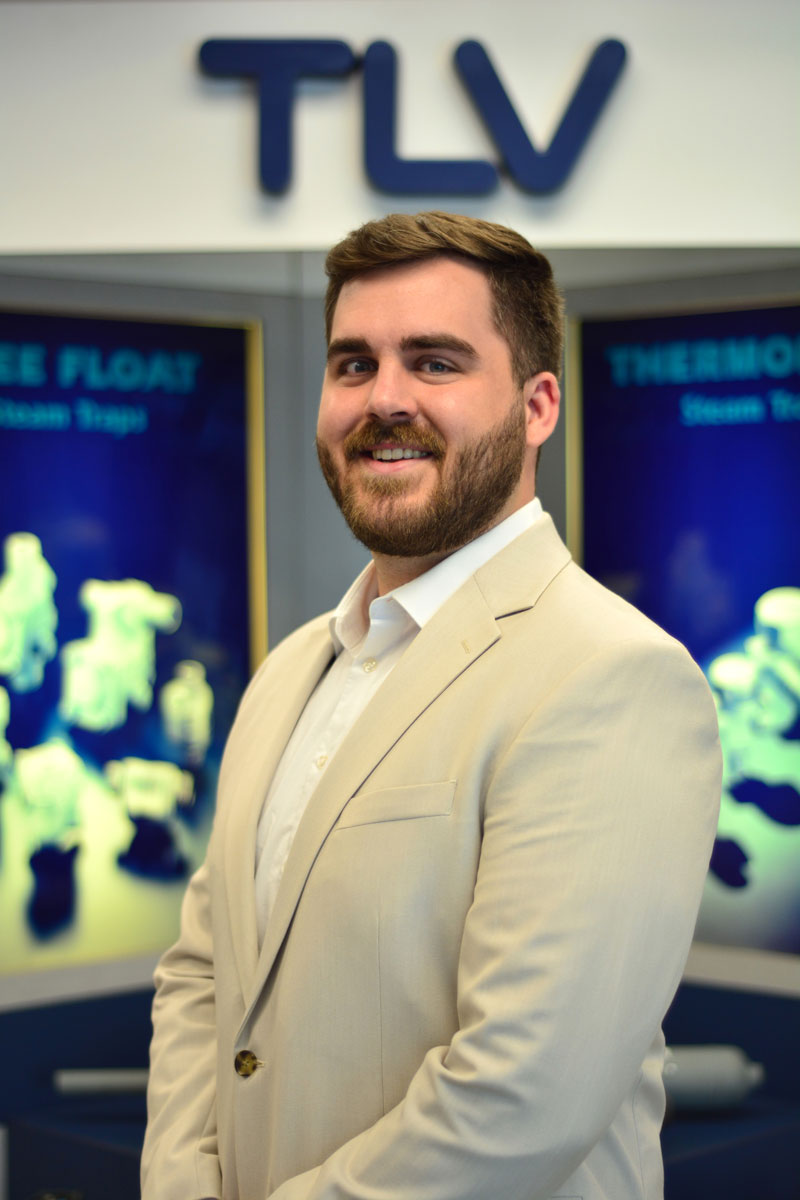
We have been using the methodology of the API 581 Risk Based Inspection guideline and applying that to steam assets, and now the industry is adopting it as part of the new 4th Edition of the API 581 guideline to make it standard.
—Norm White, President, TLV Corporation
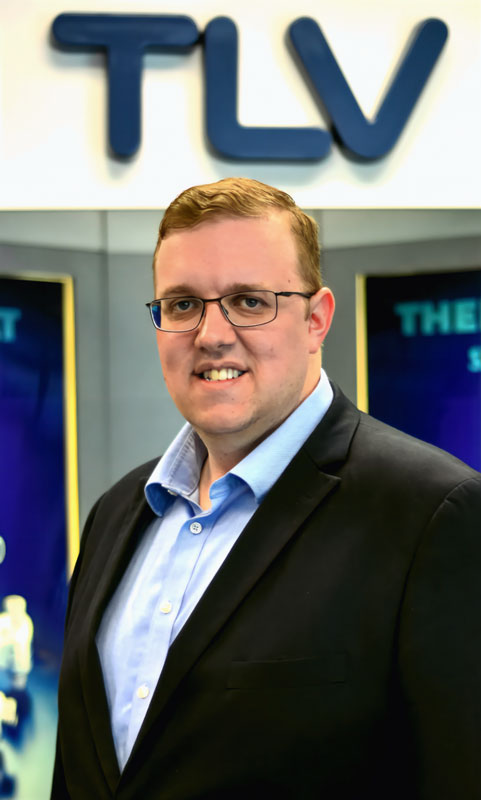
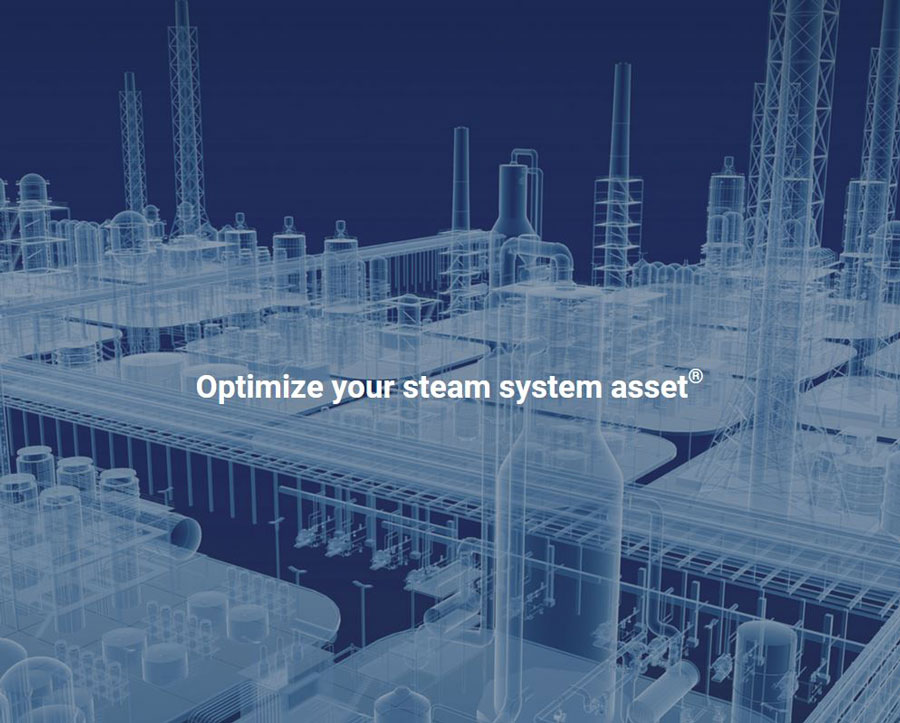
Andrew Mohr, Consulting & Engineering Services (CES) Manger, TLV Corporation, will lead a seminar, “Risk-Based Inspection of Steam Services Assets: Reliability and Energy Efficiency Go Hand in Hand.” Since its first release in the year 2000, the API Recommended Practice 581 has provided methodology for performing Risk-Based Inspection (RBI) on petrochemical plant assets such as pressure vessels and piping, storage tanks, heat exchanger tube bundles, and pressure relief devices. The forthcoming release of API 581 (4th edition) will now include and address RBI for steam system assets such as steam traps, mechanical pumps, control valves, steam lines, steam turbines, heat exchangers, distillation tower/columns, steam-assisted flares, and steam tracing systems.
This presentation will introduce the concept of RBI of steam system assets, as well as provide specific examples of how to conduct RBI on steam system assets using TLV’s Steam System Risk Mitigation (SSRM®) program and software. The presentation will show how the impact of energy + reliability + productivity can be quantified when evaluating steam system assets for maintenance and capital improvement projects.
In the exhibit hall, TLV invites attendees to learn about applying a risk-based inspection process to steam-based assets. They can run case studies through a computer. “And, as always, we’ll have a science presentation showing some examples of moisture separation and air venting so people can see these things in person,” says White.
“While we’ve always worked with the engineering and the maintenance teams and the people operating the steam utility,” says White, “we’re also reaching out to the inspection groups with the RBI process. TLV would like to be the bridge between the inspection groups and the engineering and maintenance groups, at least when it comes to the management of their steam assets.”
For further details on TLV Corporation’s innovative solutions or to request a personalized consultation, please visit Explore TLV Corporation. Discover how TLV can help you optimize your steam system and advance your sustainability efforts.