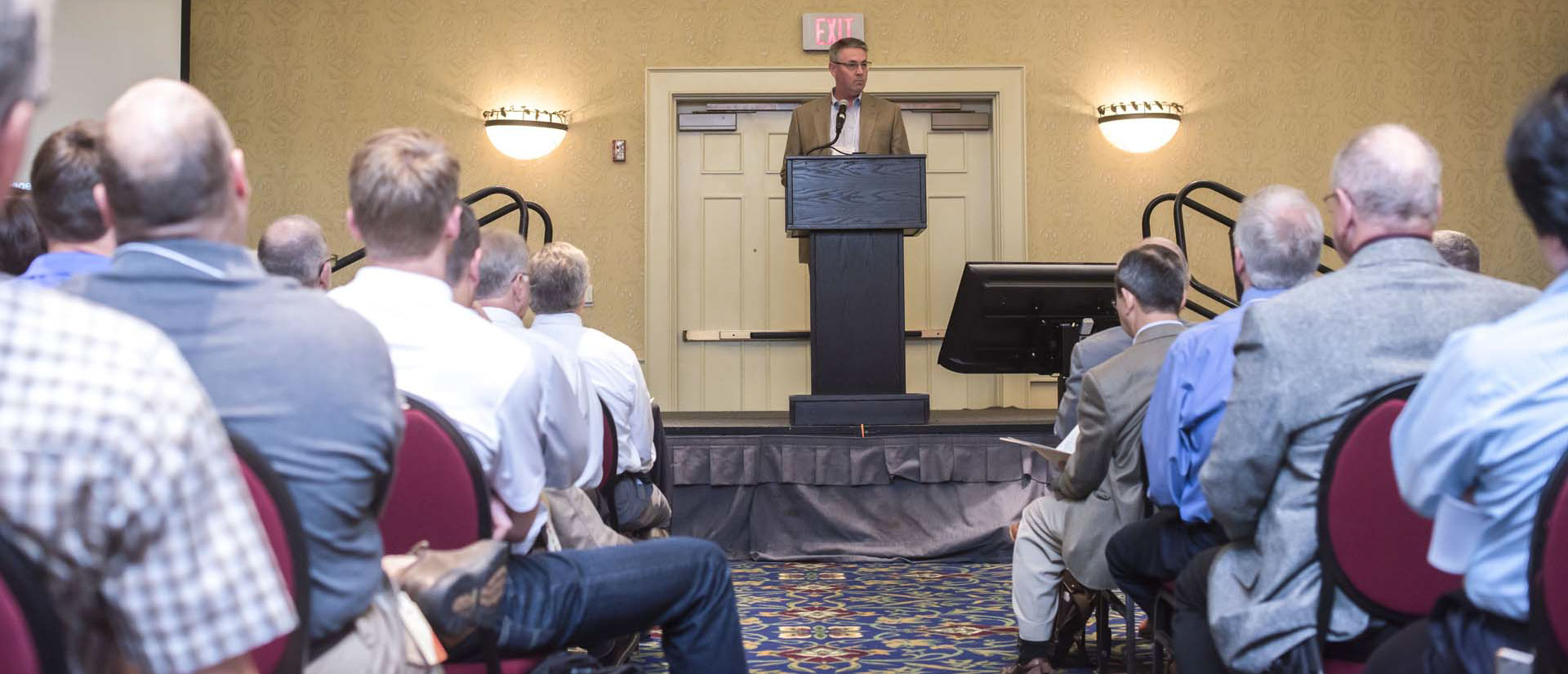
Urging a standing-room-only crowd of attendees and exhibitors to keep up with technology that’s advancing at an ever-increasing pace, Parker Smith, Eastman Chemical Co. vice president and general manager, worldwide manufacturing support and quality, began his keynote talk at eChem Expo with a quote he attributed to Pres. George W. Bush.
“You can’t do today’s jobs with yesterday’s methods and be in business tomorrow,” Parker quoted Bush as saying. The former president was reflecting on how quickly change is accelerating, Smith said. In fact, the rate of acceleration is now doubling every 11 months, he cautioned.
So much of what Americans touch at home or during leisure now carries an underlying layer of technology, Smith said. He noted that everyone in the meeting room had probably used the computing capacity of a phone that morning – for everything from checking the weather to adjusting the home thermostat remotely.
Technology follows workers to the plant, where it permeates every discipline, including mechanical, chemical, electrical, controls and robotics. “They’re all connected,” Smith said. “Technology advances by leveraging other advancing technologies.”
Eastman uses technology to focus on safety, reliability, productivity, energy management, mechanical integrity, regulatory compliance and capital optimization, Smith said, adding that “that’s not inclusive by any means.” And failing to focus that way could mean losing the capability and privilege to operate as a growing company, in his view
Moreover, a company can’t create an injury-free workplace without attention to all of those areas, Smith said. And don’t forget, he reminded the audience, that technology can play a key role in environmental compliance.
Keeping all of that in mind can present a challenge, Smith acknowledged. “You have to cast a wide net and then understand the meaning of all the pieces that gives to you,” he advised the audience.
By way of example, Smith cited recent improvements in how Eastman generates its own power – improvements that the company couldn’t have made a decade ago because the right integrated technology didn’t exist.
Calling eChem Expo a “great venue,” Smith maintained that Eastman is fortunate that the conference and exhibition convenes in its back yard. He encouraged attendees to engage with speakers, exhibitors and their fellow Eastman employees. “It’s a great opportunity to network with one another,” he said. “There are great things going on in all of our companies and businesses.”
Trio of Keynote Speakers Praise the Conference for Engineering Relevance
Five Challenges
The next keynote speaker, Ronald K. Dailey, Nuclear Fuel Services director of engineering, outlined five challenges that he counseled his audience to consider on a regular basis.
5. Knowledge Management. Managing knowledge used to require a set of procedures or a handbook, but these days it makes more sense to integrate knowledge into the coding and controls, Dailey said. That way, a plant can deliver the right information to the right person at the right time, he maintained.
4. Balance. Plants should also balance cyber security and smart technology, Dailey advised. It pays to be smart about where to place firewalls and where to air gap systems to safeguard information that’s proprietary to a business or vital to national security, he said. That’s why, in his view, engineers who innovate should consider how to implement their new creations.
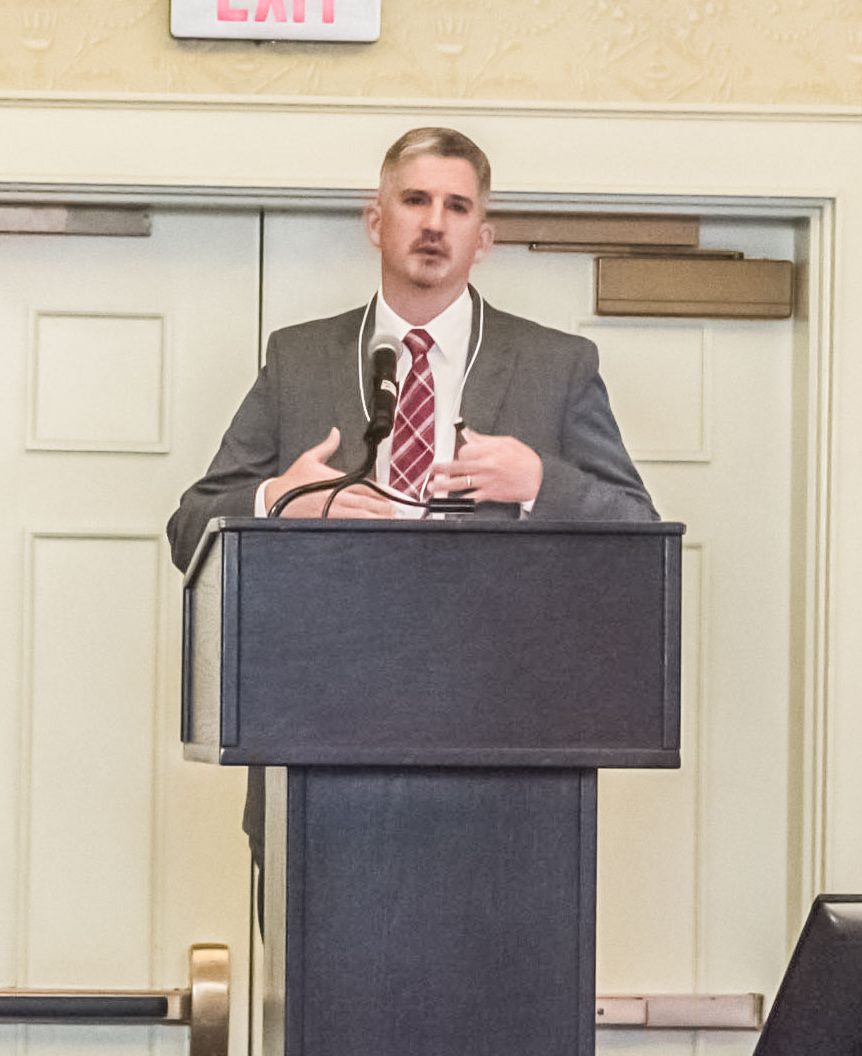
3. Collaboration. Multi-discipline teams should work together to solve problems, Dailey told the crowd. Companies and vendors also should cooperate, which can present security challenges. That can prove tricky but it’s worth pursuing a solution, he said.
2. Quality. Challenges arise in the quality of technical work, information and communication, Dailey said. As the nation becomes a more text-based society, information is becoming more concise but not necessarily more accurate or more thorough, he noted. Take time with documentation, he advised. In his view, quality should not die just because engineers are moving more quickly. Don’t rely on the next version of a product to correct flaws, he admonished the audience.
1. Cost management. In a world exploding with innovation, use care to separate what’s useful from what’s not needed, Dailey said. “What percentage of the functions in our smartphones do we use?” he asked by way of example. “Maybe 10 percent?” In the process industries, make sure to pursue value for the shareholders, he warned.
Dailey concluded by explaining that he pointedly excluded safety from the list because it should not constitute a challenge. “Safety should be viewed as how we do business,” he declared. “It has to be our behavior. It has to be our attitude. It has to be in our designs. It has to be in our discussions. It is the only we can survive, much less thrive.”
Genesis of a Plant
The third keynote presentation came from Thomas Kastenberger, Wacker Polysilicon head of engineering, who was addressing the crowd just a week after the opening of his company’s huge new $2.5 billion plant in Charleston, Tenn. “We are really proud to be operational after several years of hard work,” he said.
Kastenberger noted that it was the third time he had described the birth of the plant to an eChem Expo audience. The first time, he spoke of how challenging it was get the project underway. In his second presentation on the subject he shared the travails of slowing down the completion of the plant during the recession. Finally, the ribbon had been cut and production had begun.
Some 19 million hours of labor have gone into conceiving of and building the plant, Kastenberger noted. “We built a little city, actually,” he said of the multiple interconnected structures that came together for a single purpose – to produce polysilicon, which is used to make photovoltaic solar panels. “So we’re a contributor to getting more sustainably produced energy,” he said.
Looking out over the audience, Kastenberger thanked those in attendance who represented the many companies that contributed products, expertise and labor to designing, building and commissioning the plant. “You helped us get to where we are today,” he said.
Other suppliers – those who provided substandard equipment for the plant – wouldn’t deserve those accolades. Three examples illustrate the problem of poor quality, Kastenberger said.
In the first example, heat exchangers came with deformed tubes and unacceptable welds. Second, a compressor contained a nut and bolt where they did not belong. In the third example, a protective shield wasn’t installed and corrosion quickly set in and caused leaks.
“These are examples of how life became more difficult than it was already on a project of this size,” Kastenberger said. “Luckily we also had contractors and partners who helped us fix all these things. So they didn’t really become show-stoppers.”
The point of presenting the problems at the Expo was to show how expensive they can become, Kastenberger said. “It’s too costly for us and too costly for the companies providing these services,” he maintained.
In his view the answer lies in collaboration. “We can only be successful if we are working together,” Kastenberger told the crowd. “We need to challenge each other, and we need to understand the scope required.”
[apss_share]