Industry leaders discuss connecting people, processes and technology for operational excellence.
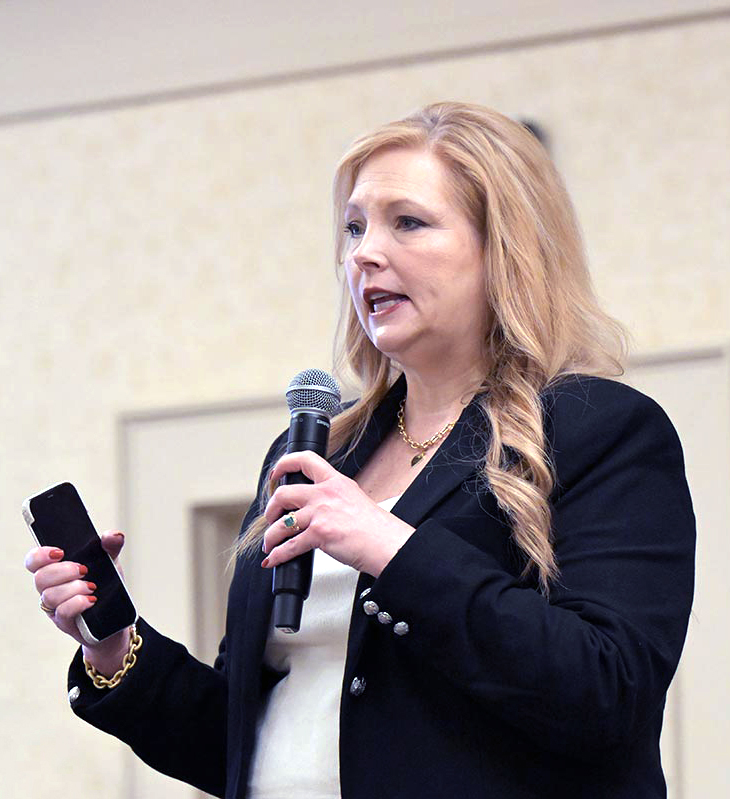
Three industry leaders spoke about connecting people, processes and technology for operational excellence on Day 2 of the eChemExpo.
Jan Shumate, who leads the worldwide engineering and constructions solutions organization at Eastman Chemical Company, moderated the panel. The speakers included Erik Volkerink, CEO and co-founder of Trackonomy Systems; Keith Chambers, vice president for manufacturing solutions at AVEVA; and Alexander Pfalzgraf, senior digitalization consultant at Siemens.
“They’re each innovators in the field,” Shumate said while opening the session.
In all, I think when it comes to working on operational excellence, I think what you should do is build a framework or program about operational excellence. You need to formalize all of this so that the whole organization stands behind (it),”
—Alexander Pfalzgraf, senior digitalization consultant at Siemens
During the discussion, Chambers spoke about smart factories, which involve modern technology, such as artificial intelligence, to analyze data, drive automated processes, and learn.
“And they defined it as the application of technology to improve technology and standard work to improve efficiency and flexibility for agility,” he said.
According to Chambers, things have changed considerably in the last 10 years, with smart factories becoming more “people-centric.” “But what’s really involved now is a much more people-centric view,” he added, emphasizing the shift in focus.
He also discussed transformation in the industry, highlighting the evolution of processes. “In terms of processes, again, companies have very well-developed processes, and there’s processes out in the public space that help companies achieve operational excellence. And all of these kind of processes make you lean” and assist with “coming out ahead,” he explained.
Chambers pointed out that when people are involved, things become a “little tricky.” He outlined three steps to improve factories: enhancing worker productivity, particularly of the operators; improving individual performance, “meaning how can you help them to improve their performance in the execution of their jobs;” and enhancing team performance.
“How do we create a culture, culture’s a very overused term, but how do we create a culture of performance?” he asked, probing deeper into the concept of workplace culture. “In other words… the people and technology processes that help improve how collectively everyone can perform together.”
Chambers also discussed how technology facilitates advancements in smart factories. The first area focuses on the flow of information and connecting people. “So, collaboration, which is increasingly a social thing, is how you connect the people together,” he said.
The second role of technology is in aiding job performance. He emphasized the transformative potential of artificial intelligence: “Technology, such as artificial intelligence, can help us sense things far earlier than a person would.”
“The ability to sense things using AI in a way that operators can’t and then from a response perspective, again, this idea of information flow and a system that’s social and collaborative to make sure so the decisions that have to be made and the actions that have to be taken are communicating effectively to everyone,” he explained.
In conclusion, Shumate thanked Chambers for his insights into the evolving idea of corporate culture in the context of modern smart factories.
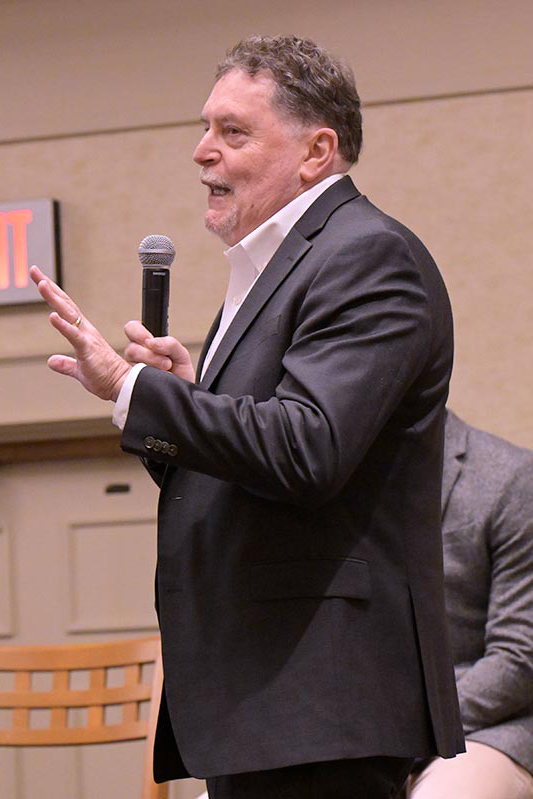
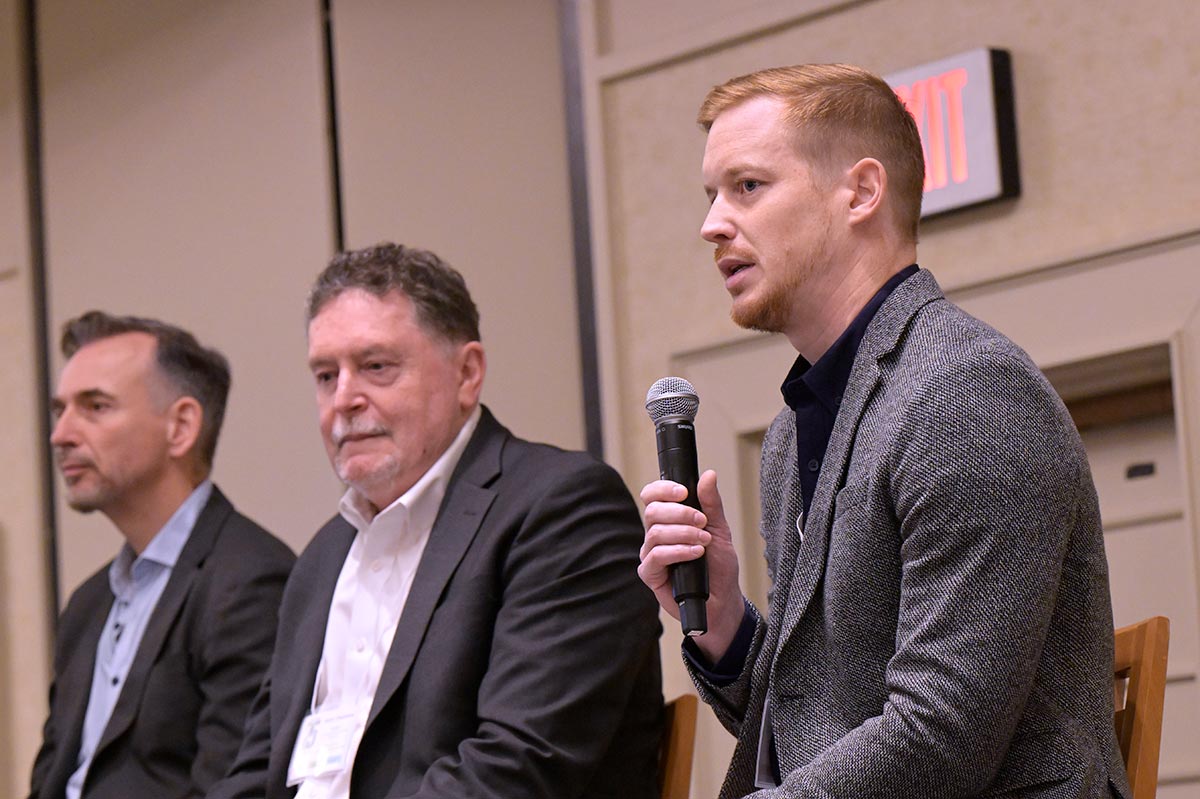
So, collaboration, which is increasingly a social thing, is how you connect the people together…
—Keith Chambers, vice president for manufacturing solutions at AVEVA
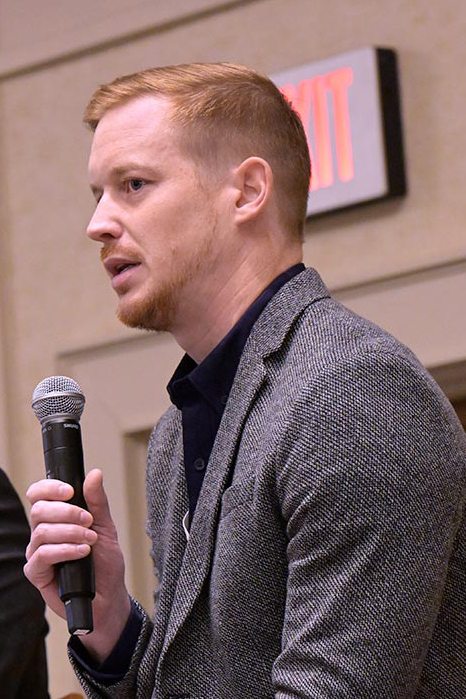
“Maybe you can help us explore how to pull all that together and really unite people from different places towards (building a culture of operational excellence),” Shumate asked Pfalzgraf.
Pfalzgraf responded, “I like that a lot because for me this is one of the most interesting key factors to achieve our personal success. You have to build that culture, you have to enable change, you have to enable people and organizations and you also have to motivate them because if nobody is motivated then nobody is going to achieve anything,” he elaborated on the necessity of fostering an engaging and empowering corporate culture.
He emphasized the importance of redefining quality in the context of corporate culture: “One thing to focus on regarding corporate culture is to define quality, not as a product attribute, but as something that is defined as customer experience,” he said. This approach embeds the quality topic into everything, ensuring everyone knows their role in contributing to quality.
“In all, I think when it comes to working on operational excellence, what you should do is build a framework or program about operational excellence,” Pfalzgraf suggested. “You need to formalize all of this so that the whole organization stands behind it,” he added, highlighting the need for structured programs to support operational excellence initiatives.
Shumate thanked Pfalzgraf for touching on the technology element that supports operational excellence, acknowledging the crucial role it plays in enabling the discussed changes.
In an ideal world, we've met in the future where you have AI skills around that process. And the moment somebody violates the process” …”he gets nuts like, ‘oh, yeah, I wouldn't do that.
—Erik Volkerink, CEO and co-founder of Trackonomy Systems
Asking Volkerink, Shumate said, “Dr. Volkerink, I know you’re seeing a lot of cutting-edge developments. Can you expand on how you see technology supporting operational excellence and bringing all these components together?”
Volkerink responded with confidence in the process-driven approach, “I fully believe what they were saying about people’s process, I think if you improve the process, you have a better impact than people necessarily, right,” he said. “So, Keith is looking at how you have a great process, how do you enforce it with these limitations, right?”
He elaborated on the integration of technology in enforcing processes, “So in an ideal world, we’ve met in the future where you have AI skills around that process. And the moment somebody violates the process, but in five seconds, he gets nuts like, ‘oh, yeah, I wouldn’t do that.'” This illustrates a futuristic scenario where AI directly interacts with process adherence.
Volkerink also discussed the broader implications of technological advancement in operations, mentioning, “most are thinking around mission control and sensory computing.” He highlighted the increasing role of sophisticated computational systems in operational settings.
He added a crucial insight about maintenance and operational costs, “The cost of fixing versus the time of detection. You know, it doubles every minute, almost, right,” Volkerink said, emphasizing the exponential impact of timely problem detection on cost efficiency.
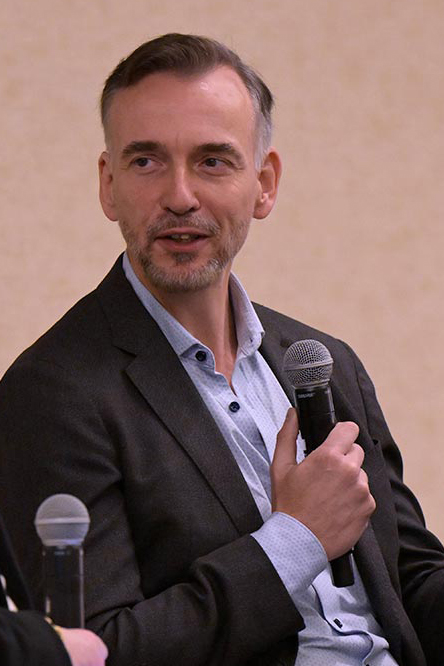