Technology to Transform the Everyday
Welcome to the industrial metaverse. It’s a virtual world almost impossible to distinguish from the real world, an immersive space where people and AI can collaborate in real time to solve real-world problems.
Siemens technology is often hidden but is literally everywhere, working behind the scenes, helping customers in the chemical industries make plants safer, more comfortable, and more energy efficient.
Siemens Digital Industries is a driving force in the digital transformation taking place in the process industries. Based in Nuremberg, Germany, it has a workforce of around 78,000 employees worldwide and offices in all 50 states of the United States.
Automation and Digitalization play a key role in accelerating advancements in safety, operations, and sustainability
—Mayank Patel, Industry Strategy Director – Chemicals, Siemens
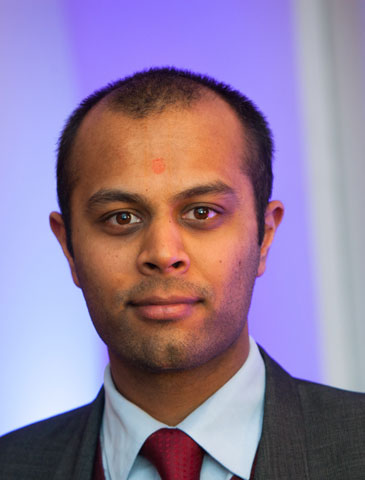
“Automation plays a key role in accelerating advancements in safety, operations, and sustainability,” says Mayank Patel, Industry Strategy Director – Chemicals, Siemens. “If we look at safety as one example, creating virtual models of the real world via digital twins is really a way for engineers to test and optimize safety processes or procedures before limiting them, and therefore minimizing the risk. If you look at sustainability as another example, I think energy-efficiency solutions can help optimize what you’re consuming, across many units. And automating manual tasks and leveraging data analytics with technology can really improve operations and efficiencies.”
On the exhibit floor, Siemens Digital Industries will feature all aspects of the process lifecycle. “Seeing the R&D process for products will help attendees visualize technologies that can help them achieve newer goals of sustainability and the incorporation of digitalization while also addressing day-to-day challenges like reducing bottlenecks or looking at ways of improving operations from a throughput perspective or otherwise,” says Patel. “Further along the cycle, we’ll start looking at things like virtual commissioning and engineering, so the community can explore those digital environments that support the commissioning of new processes, but also look at management workflows and how to do data exchange or transfer between different stakeholders via commerce.
“And then finally going through to the operational and maintenance stage, attendees can explore things that developed at the early stages. For example, in the R&D stage, in terms of modeling, simulation can be leveraged at the latter scales in operations where you have a completely different user community – and when what you’re looking to achieve from an operations perspective compared to an engineering or R&D perspective is completely different.”
Siemens will be hosting a seminar about the future of work and sustainability, called “Front Line Worker Training Through Extended Reality Applications.” It will be led by Iiro Esko, Chemical Industry Manager, Siemens. Digital twins can change the frontline working environment from a training and operations perspective, leading to enhanced safety and operational excellence. Attendees will learn what technologies are available to support virtual training solutions via avatar-based platform visualization techniques. They will also learn how to leverage augmented reality to empower workers with real-time information and improve that efficiency and safety angle. As well, the seminar will demonstrate some of the workflow methods for gathering necessary data to then provide to stakeholders like your suppliers to minimize any transformation costs. Attendees will also discover how to convert prevalent 3D models, engineering data, and supply information into more advanced applications. The goal is to demonstrate how to empower these frontline workers with the technology that’s available today.
Digitization of the industry has happened in waves. “Back in 2018 and 2019, we saw that management on the customer’s side were pushing to find out how they could apply digitalization to their processes and product portfolio, but it wasn’t really trickling down to the workforce on the ground to tangible activities,” said Patel.
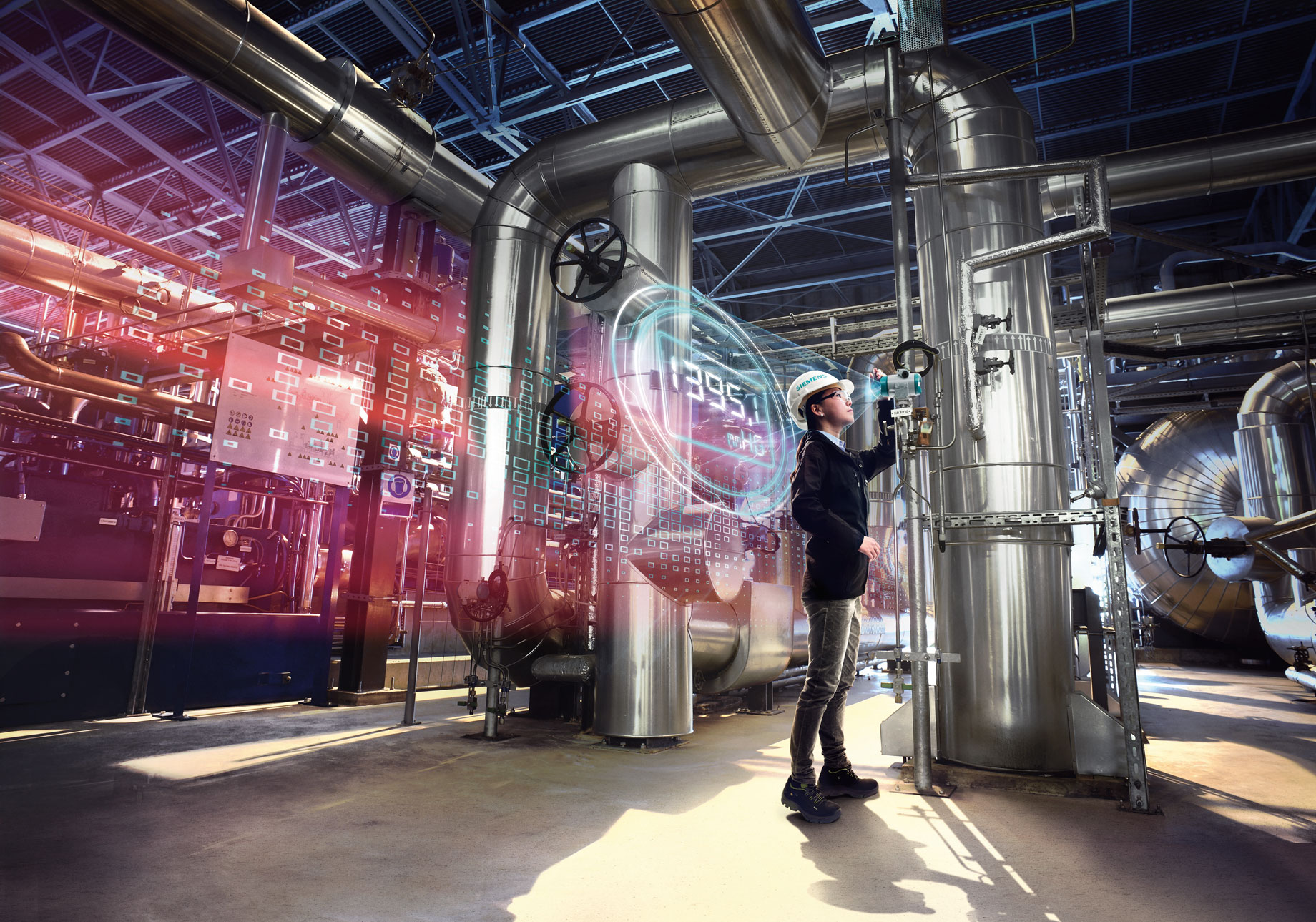
In the industrial metaverse people and AI can collaborate in real time to solve real-world problems.
Management pushed to find out how we could digitalize the way we do things, but it wasn’t really trickling down to the guys on the ground.
—Mayank Patel, Industry Strategy Director – Chemicals, Siemens
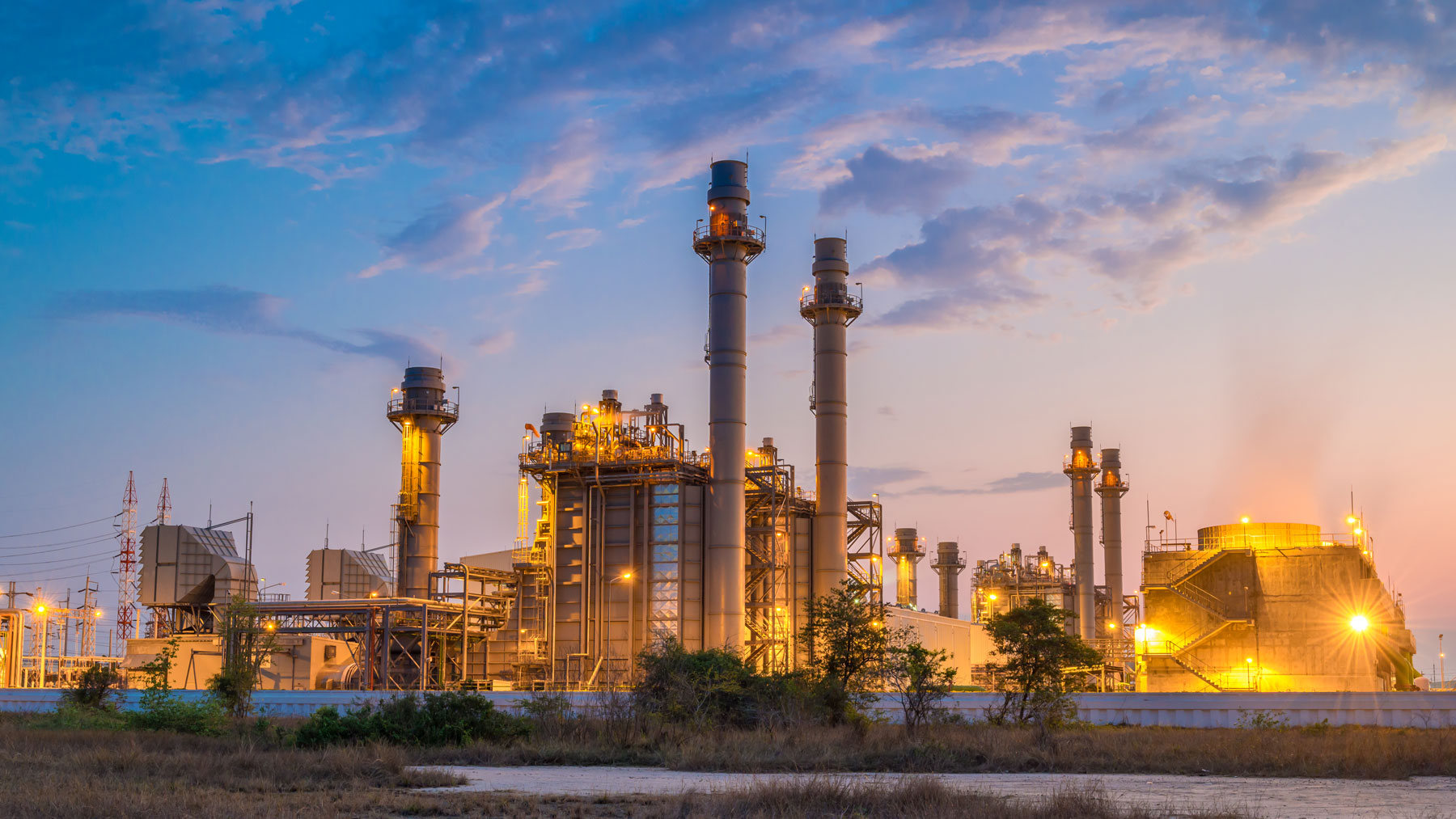
Alex Pfalzgraf, Senior Digitalization Consultant, and Jose Roberto Manzano, Head of Process Automation Software North America, Siemens will team up to present “How to Live Your Digital Journey.” Every company in the chemical industry has realized the need for digital transformation to increase efficiency, security, and productivity. But to do this, they need to leverage technologies such as artificial intelligence, smart monitoring, and data analytics. At first, it can seem overwhelming. Attendees will learn strategies to get employees on board and build a culture of continuous adaptation. The key is to look at many projects that are embedded within the way that companies work, and to learn from experience and look for improvements and identify possible adaptations.
“Sustainable Digitalization: Where the Recycled Rubber meets the Road to the Future” will be led by Don Mack, Industry Manager, Siemens. This seminar will cut through the buzzwords and dive into the practical applications that are available today to achieve sustainability goals. Mack will share several real-life examples of using Industry 4.0 technology to produce chemicals in a more resilient and responsible way including carbon footprint reduction, energy efficiency, and recycling. Discussion will focus on how to tackle some of the challenges because some of these processes can’t exploit the traditional scale up or chemistry learnings.
Attendees can also learn about recent Siemens collaborations at the Siemens booth. The newly launched Siemens industrial copilot acts as a programmer and revolutionizes the way machines are operated. Siemens partnered with Amazon Web Services to make the power of generative AI accessible to all by integrating with Mendix, a low-code platform. Until recently, AI functionality in a low-code program application has remained a challenge. But now anyone can pick a generative AI model and add it to an application with just a few clicks. Mendix makes it easy to connect to multiple Amazon web services machine-learning models, dropping them inside applications to start reimagining customer experience, products, and processes.
As Siemens technology seamlessly integrates into the fabric of our everyday lives, it serves as a powerful force, enhancing safety, comfort, and energy efficiency in chemical plants and beyond.
For a deeper dive into how Siemens is pioneering the future of digitalization and sustainability in the chemical industry, visit our Specialty Chemicals portal.
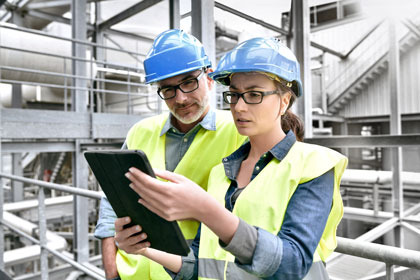
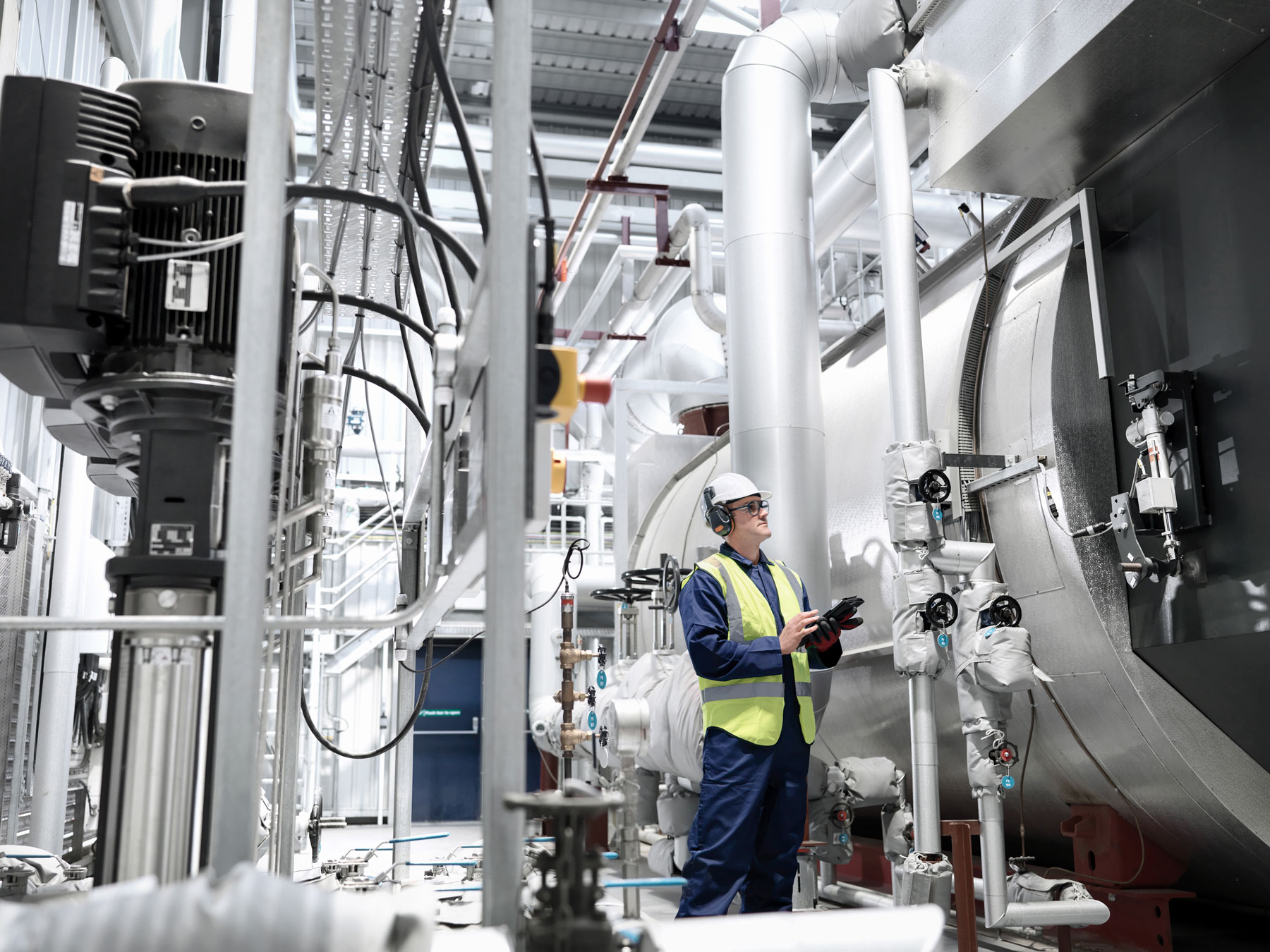
Mendix, a low-code platform, makes it easy for anyone to pick a generative AI model and add it to an application with just a few clicks.