Experts talk about plastics recycling technology
This photo shows a 12,000 pound demo unit being unloaded at the dock for eChemExpo. AUTOSORT is TOMRAs flagship sorting solution which utilizes a combination of material, color, metal and 3D object detection to sort and purify feedstocks for recycling. The unit was delivered to eChemExpo to showcase the TOMRA technology as it pertains to feedstock preparation for Chemical Recycling
By Robert Sorrell
“Plastics recycling is here today” declared an Eastman Chemical Company representative back in mid January of 2022 as a follow-up to a Stakeholder Interview previously conducted. That declaration followed up with a list of suggested companies to invite as exhibitors and possible speakers at eChemExpo 2022, which was less than three months away.
So on very short notice, eChemExpo organizers pulled together a highly relevant program that included 10 participating companies. Six of the selected innovation leaders were part of the seminar program described in this article. Other exhibiting participants included Weima, Herbold, Gneuss, and Coperion K-Tron.
Plastics recycling experts from around the world gathered in Kingsport TN for eChemExpo 2022 to speak on new technologies and creating a circular economy.
The gathering follows last year’s announcement from Eastman Chemical Company that it would build one of the world’s largest plastic-to-plastic molecular recycling facilities at its site in Kingsport. Through methanolysis, the $250 million facility will convert polyester waste that often ends up in landfills and waterways into durable products.
Utilizing the company’s polyester renewal technology, the new facility will use over 100,000 metric tons of plastic waste that cannot be recycled by current mechanical methods to produce premium, high-quality specialty plastics made with recycled content, according to an Eastman press release.
The company has committed to recycling more than 250 million pounds of plastic waste annually by 2025.
Exposition planners called upon some of the world’s most knowledgeable plastics recycling experts and industry leaders to speak during a new session track on this hot topic.
Tomra’s ambition is to increase collection by the year 2030 to 40 percent, compared to the 14 percent today
—Nick Doyle
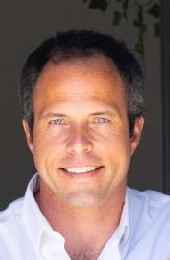
Sorting Materials
Tomra is one of the leading companies in the industry. With about 4,300 employees worldwide and about $1.2 billion in revenue from 2020, the company specializes in sorting and collecting plastic waste for recycling.
The company features multiple divisions, including material recovery, sorting, and collections. Within those divisions, company representative Nick Doyle said the company also has a reverse vending division “where consumers go up, put a bottle into the machine and get money back.”
Doyle spoke about Tomra’s scanning technology that is used to identify and sort plastic materials.
Tomra uses a belt fed system and a chute fed system to sort items. The belt fed system is typically seen over at MRFs, or a materials recovery facility, and is used at recycling facilities. The company’s flake sorting unit is used exclusively at plastics recycling facilities as a final purification step after wash and grind to get those to decontamination and extrusion, Doyle said.
About 14 percent of all consumed packaging is recovered for recycling, a statistic referred to several times during the session. The remaining 86 percent goes to the landfill, oceans, and elsewhere.
“And this is the challenge that we’re seeking to overcome,” Doyle said
Tomra’s ambition is to increase collection by the year 2030 to 40 percent, compared to the 14 percent today.
“This is the role that we play here, where we take material from the MRF, purify it, and then turn it into the clean bales and then get it into the color form here,” said Doyle, describing Tomra’s process.
“And it’s very important to have a pre-sort because in the world of feedstocks you must have the cleanest feedstock in order to get the best yield in your process,” he said. “And so we specialize in that feedstock purification stuff.”
Tomra developed the circular economy division about two years ago.
And the purpose of this was to provide, become more of a resource for our customers outside of our general business scope, where our general business scope, which has been working with recyclers and plastic recycling,” Doyle said, “but now with our circular economy division, we are actually consulting and advising with larger companies, consumer product manufacturers, beverage companies, to help them better identify opportunities for circularity within their existing supply chain and also to navigate the existing infrastructure and players to help them get the appropriate solution and dial right into the existing supply chain.”
Tomra takes real-time analysis of materials to improve the process, which is valuable in terms of plant performance and contractual obligations, Doyle said.
This leads to improved processes and sustainable circular economy.
“We unlock unique potentials, we develop scaling up initiatives, and then we help create markets in the business cases so that these materials can continually be recycled,” Doyle said.
Our mission is a big mission of a world without waste
— Jay Goldin
Robotics Technology
Another company, AMP Robotics, also identifies, sorts, and separates plastic waste for recycling.
“Our mission is a big mission of a world without waste,” said representative Jay Goldin.
The company looks at waste as “all that valuable material there that’s sitting on the ground waiting for somebody to pick it up.”
“When it’s separated and refined, it has value,” Goldin said.
First, the company supplies its technology and systems into existing infrastructure.
“If you put your stuff in a blue bin, it goes to a MRF,” he said. “That MRF may or may not have our equipment in it.”
Secondly, the company operates its own technology and infrastructure in its own facilities. “But basically, what I’m talking about today is smarter systems, superior sorting and better materials for recycling,” Goldin said.
The company uses neural networks, machine vision, and artificial intelligence to sort and categorize waste. It can handle two pieces of waste per second, Goldin added, and the company is working to improve that rate.
AMP Robotics uses robots, which are sourced from other partners, to pick through the materials. The robots work with a variety of materials, including polypropylene and PET (or polyester). New categories of materials can be added into the company’s systems, Goldin said.
Goldin said his company would like to learn from others on how to better handle materials, especially those that are difficult to identify and recycle.
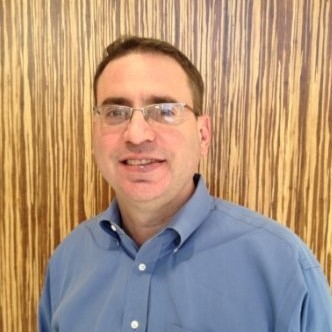
The good news is that fundamental building blocks for technology exist. We don’t have to completely reinvent the rocket
—Mark Bauman
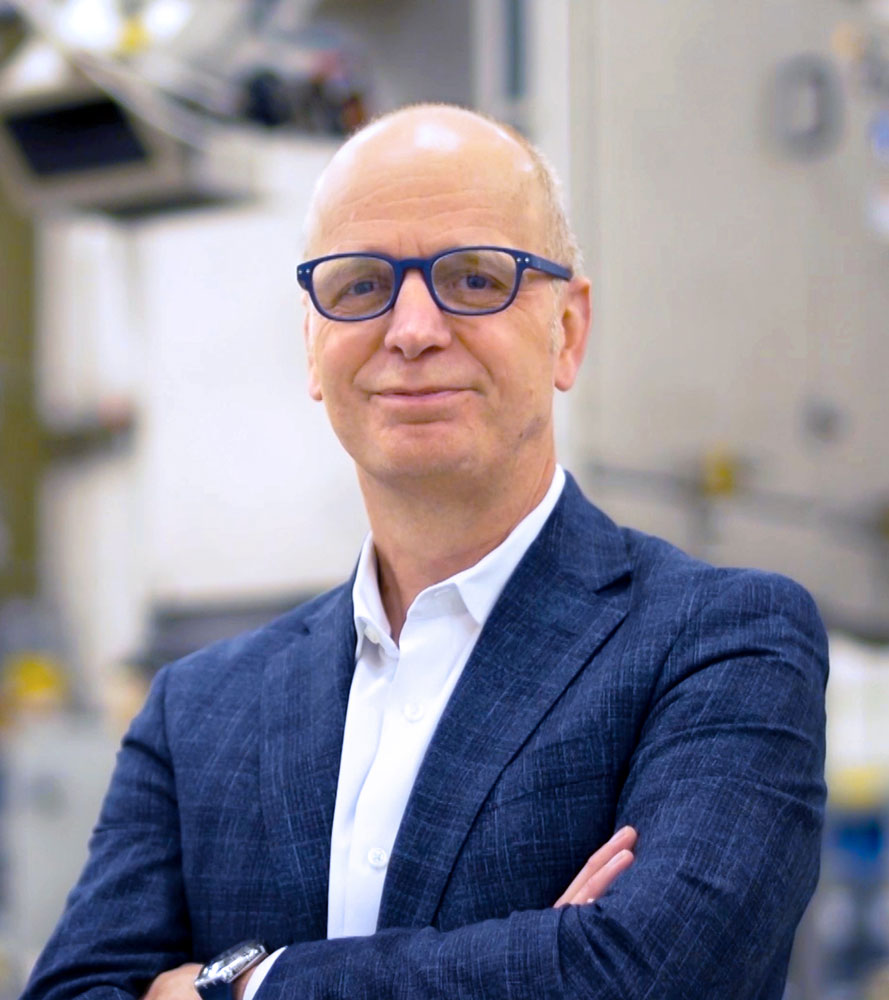
Fundamental building blocks
The MAAG Group, which plays a key role in enabling a more circular economy for plastics, provided an overview of its equipment and philosophy regarding plastics recycling. The equipment covers the entire plastics value chain and helps to introduce used plastics back into the economy, according to the company.
Martin Bauman, the company’s vice president for U.S. operations, explained MAAGs pump systems.
“The good news is that fundamental building blocks for technology exist,” Bauman said. “We don’t have to completely reinvent the rocket.”
Bauman shared information about the company’s PET recycling system, as well as other types of recycling systems.
Quality Materials
Founder Nathanael Lortie represented Canadian manufacturer Eagle Vizion, which produces advanced sorting equipment, during the session.
“We are originally a company that manufactures optical sorting equipment,” Lortie said. “I’m going to go specifically into what we call the advanced characterization of plastic for post-consumer plastics.”
In 2012, Eagle Vizion leaders decided to orient the company towards advanced identification in plastics recycling, Lortie said.
“What we were seeing in trends was packaging was changing and you’re getting more and more polymers, packaging with multi layers, contaminants that wouldn’t take out of your screen because for them it was still a PET. But for the end users, it wasn’t the case anymore,” Lortie said.
Since 2012, Eagle Vizion has developed sensors where a company can detect the polymers that are being fed upfront, and also towards the end of the stream, he said. “We developed squared technologies combined with AI to help combine the two technologies for better sorting, because as we go through packaging throughout the years, not only is the material getting dirtier, even though it’s still a bottle, for example, you still have contaminants that will affect your stream downstream.”
Eagle Vizion also has flake sorting technology that is dedicated to identify and sort materials. The flake analyzer is the core of all of the company’s equipment, Lortie said.
Lortie said the topic of circular economy, which goes hand in hand with plastic recycling, has been “going on for years.”
“People want to go from bottle to bottle,” he said. “They want it to go recycle as much as they can and reintroduce it. Now, more and more brands want to have the recycle information on it. The problem is there’s more demand than there is product.”
Lortie said the industry needs to optimize collection.
“We have to improve on how to separate it before it’s sent out,” he said. “The problem that comes with that is the quality of the PET is dropping in certain aspects of it because it’s combined, it’s co-extruded, it’s multi-layered, it’s packaged differently.”
Getting the best quality material is the biggest issue right now, Lortie said.
Italian and German technologies
Frederic Blanchard with Sorema spoke about his company’s prolific efforts in Italy to recycle plastic waste. One of the company’s facilities in Europe recycles more than 2.8 million tons a year in plastic. The company serves customers worldwide.
Nikolas Wolf with Sesotec, also shared information about how his company can identify and sort plastic materials. The business provides machinery to companies around the world to recycle plastics and remain sustainable.
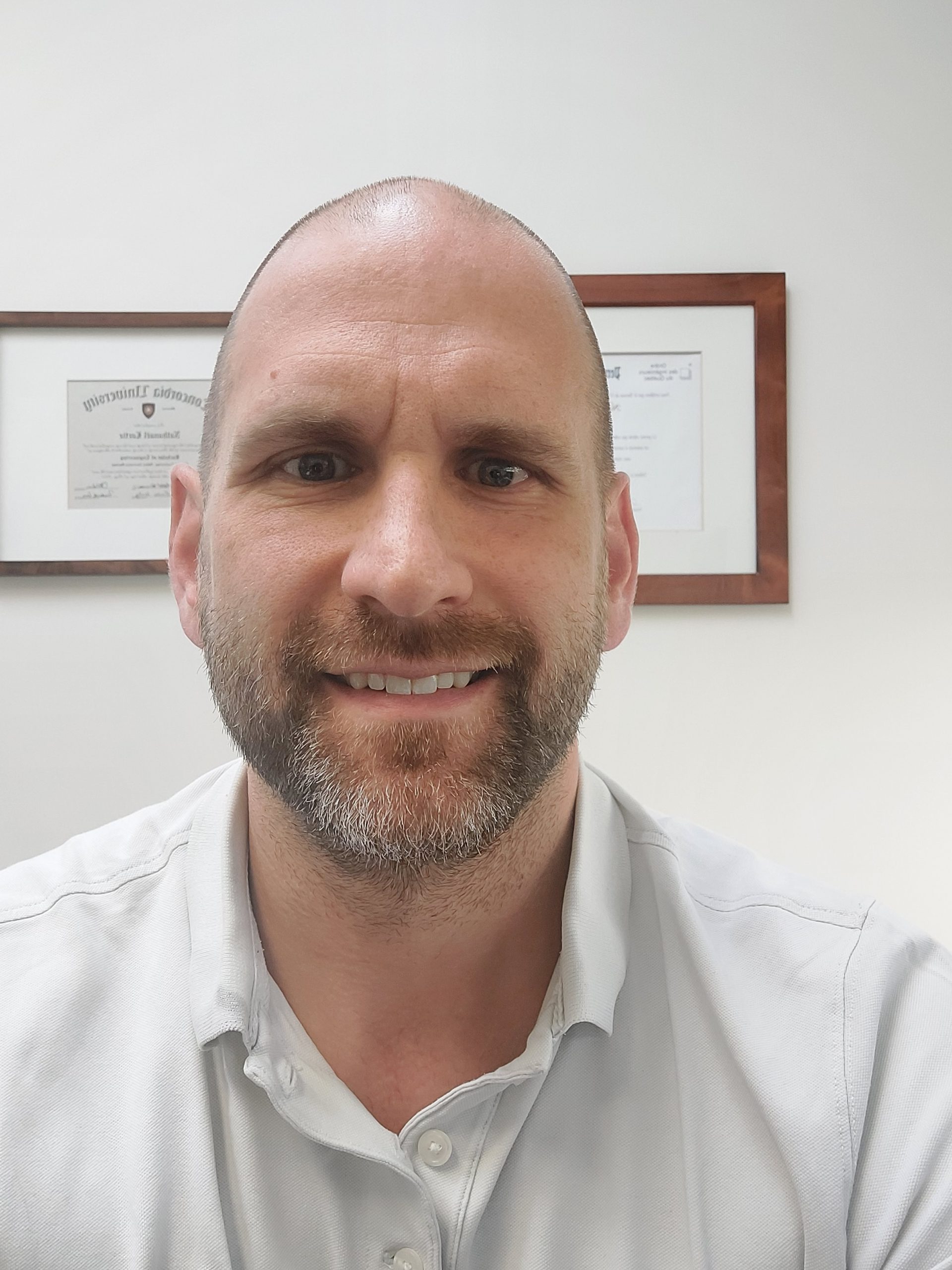
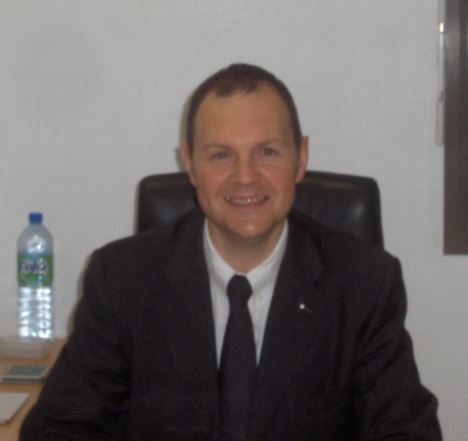
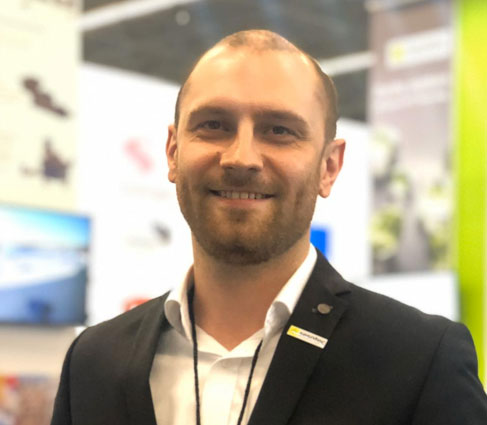