A Single
Source
Thorpe Combats Both Heat and Corrosion
Thorpe Specialty Services Corp., a company incorporated in Texas in 1954, offers the convenience and accountability of a one-stop contractor, supplier and manufacturer of refractory and corrosion products, equipment services. With other companies, it’s either refractory or corrosion – but not both.
“No other company offers this complete set of services,” declares Miles Mohnkern, Thorpe Specialty Services vice president of technical services. The Thorpe approach results in “single source responsibility” and a single point of contact for plant management, he claims.
To share ideas on those subjects, Thorpe travels to plants to present day-long seminars that concentrates on refractory services for half a day and corrosion services for the other half, Mohnkern says. That cuts travel expenses for the plant and spares employees from having to travel to hear a seminar, he maintains.
The Thorpe approach results in “single source responsibility” and a single point of contact for plant management.
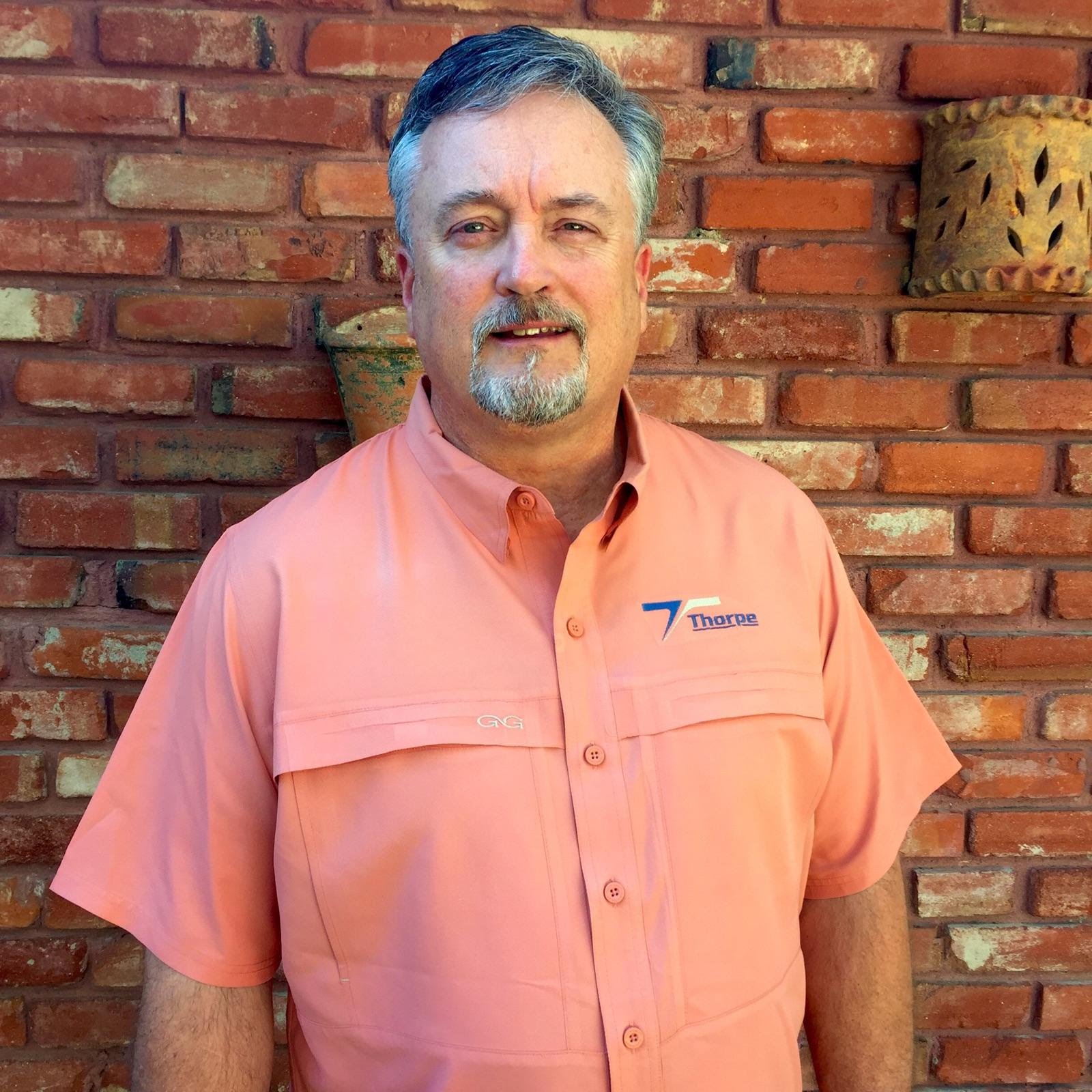
What plant people hear about in those day-long meetings centers on “refractory solutions,” which refers to heat resistance, and corrosion solutions, which focus on specialty non-metallic liners, piping and tanks, Mohnkern says.
Thorpe also plans to bring that knowledge to two eChem Expo sessions. In a seminar titled “Engineered Solutions for Fired Heater Reliability,” attendees will learn about Thorpe’s refractory enhancements of high-temperature cracking furnaces at the Eastman Chemical Co. plant in Longview, Texas, and at other plants, says Keith West, JT Thorpe senior vice president of special projects.
Thorpe manufactures Z-BLOK ceramic fiber modules to line those furnaces, which typically operate at 2100 degrees Fahrenheit West notes. “There’s a lot that goes along with that, like burner blocks, tube shields, peep-hole blocks, floors and linings in the bottom,” he adds.
To engineer those solutions, Thorpe begins by producing drawings and continues the process through installation and maintenance, West says. “That’s a big part of our business on the refractory side,” he notes. “We know gasification is big at the Kingsport plant, and Thorpe has decades of experience in complicated, severe service brick construction, including solid and gas-fueled gasifiers.”
“No other company offers this complete set of services.”
Miles Mohnkern
Thorpe Specialty Services vice president of technical services, on offering both refractory and corrosion services
This internal clarifier received new Thorpe tank Lining.
In another eChem Expo seminar,
titled “Innovative Corrosion Resistance Internal Tank Linings” Thorpe intends to cover tank linings, concrete coating, Fiberglas and laminates, according to Mohnkern. “All these are corrosion-resistant systems in lieu of metals,” he maintains.
By eliminating metals, Thorpe has enabled Eastman to take down systems at Longview for cleaning once every three years instead of needing the annual cleanings formerly required Mohnkern says. That change on the clarifier project has saved Eastman about $12 million, he notes.
But Thorpe doesn’t deal only with new equipment. To keep aging metal systems operating at Longview, Thorpe performs FRP overwraps, Mohnkern continues. “We take existing lines running until they have time at their next outage or they have the finances to replace the system,” he says.
So Thorpe is establishing a history at Eastman’s Longview plant. The corrosion work has been underway there since 2014, says Mohnkern, and the refractory work started in 1999, West adds. A supervisor is stationed there permanently, and Thorpe’s presence there grows to 20 to 50 people when jobs demand ramping up, he notes.
Thorpe has also performed work at other Eastman plants in Texas, Alabama and Arkansas, Mohnkern continues, noting that contact has been made at the Tennessee plant. “We have met with some of the capital purchasing guys in Kingsport,” he notes.
Thorpe has enabled Eastman to take down systems at Longview for cleaning once every three years instead of annually.
The discussion of corrosion control should find an attentive audience at eChem Expo. Stakeholder interviews conducted by eChem Expo in the months leading up to the conference and exhibition have revealed great interest in the subject of dealing with corrosion. Retired Eastman executive Parker Smith noted in the past that corrosion remains an ongoing concern.
At Thorpe’s eChem Expo seminars, West hopes to speak with plant maintenance people at the refractory session, where they’ll learn ways of solving problems and extend the life of linings. Mohnkern views the corrosion session as a destination for plant planners, schedulers, unit managers, mechanical engineers, inspectors, reliability engineers and procurement people.
On the exhibit floor at eChem Expo, Thorpe plans not only to display the company’s wares but also to focus on a safety record that’s been unblemished at Eastman’s Longview site since 1999, Mohnkern, notes. That means no injuries serious enough for OSHA to record during that 19-year period, says West, adding that “that’s very unique in this industry.”
Thorpe is not just a specialty services labor supplier but also a technology provider.
The parent company, Thorpe Specialty Services, was incorporated in Texas in 1954 and maintains headquarters in Houston and operates offices throughout the United States. It employs a permanent staff of 1,500 that grows to as many as 3,000 workers when demand for services peaks, Mohnkern says.
Thorpe Specialty Services performs work through six wholly owned subsidiaries. The primary subsidiaries include Thorpe Plant Services Inc. and J T Thorpe Co., which perform refractory and corrosion services in the United States, with Thorpe International Services Inc. handling work outside North America. In Canada, Thorpe performs refractory and corrosion work through another wholly owned subsidiary called Clayburn Services Ltd.
Thorpe’s experience in refractory and corrosion services means a lot in today’s marketplace as a new generation of engineers replaces the baby boomers who are reaching retirement age, Mohnkern maintains. It’s up to contractors to help fill the gap in knowledge that occurs with the influx of a new generation of plant engineers, West observes, and Thorpe intends to do exactly that. The company’s not just a specialty services labor supplier but also a technology provider that helps plants improve reliability and decrease long-term maintenance costs.