Safety by Design
Providing manufacturers with the greatest safety.
Teikoku USA creates sealless pumps that meet industry and regional safety standards for greater environmental compliance. Customers are free to focus on other aspects of their process because they don’t have to spend a lot of time undergoing process safety management audits.
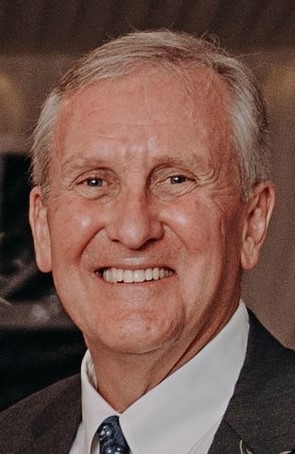
Teikoku USA is the innovator of leak-free canned motor pumps that cannot leak hazardous liquids. Their sealless pumps are used primarily in petrochemical plants, fine chemicals, pharmaceuticals, the food cooling and freezing industry, nuclear power plants, and process heating and chilling applications, boasting a 40% market share outside of Japan. They have about 110 employees across the United States.
Teikoku designs their products to meet industry safety standards. “Basically, our products safeguards our customers from a higher risk profile, because they are doing business with a company that has third-party underwriting. We’re trying to underpin all of our offerings with third-party criteria.
So, no matter the technical or design criteria, Teikoku products can be supplied underwritten by a Nationally Recognized Testing Laboratory (NRTL) to meet OSHA requirements or under standards of the American Petroleum Institute (API) or ASME/ANSI, we’re qualifying all of our unique solutions to meet our customers’ strict standards,” says Thomas Conroy, CEO and General Manager for Teikoku USA.
Teikoku does not source and assemble component technology, manufactured by others to create a finished product. Instead, says Conroy, “We literally manufacture everything that’s in it, including the motor and bearings. We have a greater portion of our manufactured costs associated with the product than any other pump manufacturer. So the onus is on us not only for mechanical standards, but for electrical standards as well. Our product is inherently safe.”
“I tell our customers that if we can mitigate the risk associated with using our product and your process, you’re free to go forward with your processes, because you know you don’t have to spend a lot of time doing process safety management audits. Use of Teikoku product will not require certain levels of monitoring or control.”
Our innovation is monitoring.
Thomas Conroy, President and General Manager, Teikoku USA
Highly-engineered, sealless pumps are manufactured in less than two weeks—the fastest production in the industry.
“You’re buying a pump and motor combined in one element. Our pumps are in many ways just like traditional motor and pump installations, but the motor is cooled by the liquid you’re pumping instead of air convection. All of our designs are double containment vessels, which makes the product inherently safe.”
This double containment provides a dynamic primary containment where the pump is spinning while, at the same time, it has a static secondary element of containment where nothing is really happening except energizing the pump driver. The motor shell actually will act, in the event of a catastrophic failure, to contain the fluid within the design pressure limits of the pump. The minute you put it in your system and energize it, you’ve got that kind of safety associated with the installation.
“If we mitigate the risk associated with using our product and your process, you’re free to move forward in full production without any additional PSM because you know, you have installed equipment that’s already designed safely enough,” explains Conroy.
On the exhibit floor Teikoku will showcase their bearing monitoring technology as a tool for preventive maintenance. They’ll also highlight their high-speed motor technology. “For most manufacturers, the slower you run a piece of rotating equipment, the longer it will last,” explains Conroy. “In our case, the faster you run it, the less susceptible the product is to failure.”
Chaitanya Sakhalkar, National Sales Manager at Teikoku USA, will be leading a seminar, Considerations for Upgrading Existing Installed Centrifugal Pumps to Liquid-cooled, Sealless Canned Motor Pumps. “We’ll discuss what you must do when you change from sealed to sealless technology, then look at the operating variables and equipment performance variables that you have to consider to make these changes,” says Sakhalkar.
James Hoffman will lead a seminar entitled, Real-Time Performance Monitoring of Operating Variables in Sealless Canned Motor Pumps. “We’ll cover the unique variables that can be measured with this technology and how it presents an opportunity to have a communicative relationship between your process and its variables. This can help make improvements to lower cost of operations costs, increase safety, and mitigate risk,” says Conroy.
It’s not just technology that separates Teikoku from their competition. “Because of the technology and its difference from conventional technology, we are the most customer focused and customer supportive vendors anyone could do business with,” says Conroy. “So if you do business with us, whether you have a project for one pump or for 50 pumps, we show up, no questions asked, no invoice in hand. We’ll help you get up and running. We train operators and we train maintenance people free of charge at our customer’s convenience.”
In the future, Teikoku will make it easier and less expensive to comply with industry standards, whether electrical, mechanical, underwritten, or layered with quality. “We’re a global company,” says Conroy.
“We’re going to be in a position where we’ll have product production elements in the product line that are built toward European, American, or Japanese standards. As a manufacturer, we know that standardization enhances sustainability, mitigates gates risk, and increases safety.”
Industry specific engineered, sealless pumps are manufactured in less than two weeks—the fastest production in the industry.